Who are you and what do you do?
My name is Dan Markovitz, and I run TimeBack Management, a consulting company specializing in the application of lean concepts to individual and team work flow.
How and when did you learn Lean?
I first got interested in lean in business school back in 1992 – not that they taught us anything about lean, but one of my assigned books was The Machine That Changed the World. It was the best book I read in business school, and not coincidentally, the only book that I’ve actually kept. However, at that time, and for many years after I graduated, I didn’t have any use for lean in my jobs, so all the ideas lay fallow.
It wasn’t until 2005 – 13 years later – when I started my own business as a time management trainer that the memories were reawakened. I realized that many of the concepts – flow, 5S, visual management, kaizen, even respect for people – are as applicable to the way individuals and teams work as they are to the way that factories operate. Since that time, I’ve been reading books and blogs and attending conferences and workshops to learn more about lean.
I still don’t feel that I have a really deep understanding of lean. Sometimes I wish I had worked at Toyota or Wiremold for a while so that I could have had a sensei to teach me.
How and why did you start blogging or writing about Lean?
I started blogging about this application of lean back in 2006. It’s helpful for me to work through my ideas in writing; I find that it sharpens my thinking. Also, I didn’t see anyone else writing about this area, and I thought it would be interesting and valuable for people who are interested in both lean and personal efficiency programs like GTD. My goal now is to develop a conversation with the lean community – and anyone else seeking improved efficiency and effectiveness – that broadens and deepens the ideas and our understanding of how lean can improve the flow of work, eliminate the common inefficiencies in communication, and reduce the wasted activity and energy in daily activities. My book, A Factory of One, is my first attempt at accomplishing that.
What does Lean mean to you?
My wife had cancer eight years ago. (She’s fine now, thankfully.) The more I can adopt lean ideas to my own work, the more time and mental bandwidth I have to spend with her. Lean is a way to ensure that I’m putting my time, energy, and attention in the place that’s most important to me. When I see people inside companies squandering countless hours, days, weeks, and months doing work of no value, I want to cry – because even if their wives or husbands or kids haven’t had cancer, I want them to be able to spend their time on things that are truly important to them – not another stupid email, another bloated PowerPoint presentation, or another pointless meeting.
What is the biggest myth or misconception of Lean?
This isn’t really a myth or misconception, but I think that companies don’t realize how respect for people translates to the white-collar workplace. For example, I see people who get work dropped on their desks at 4pm with the expectation that they’ll get it done by 9am the next day. Or a supervisor will give a direct report one more “urgent” project without any regard for the other “urgent” projects that they’ve asked the person to do. Or a supervisor doesn’t make sufficient time for coaching a direct report because they’re too busy with other work. These examples are the polar opposite of respect for people, but very few managers or executives see it that way. They see it as just the way their crazy-busy world operates, and too bad if it’s tough on the employees. But lean thinking provides a better way to operate – and more importantly, would make us think, “Hey, dropping the work on someone’s desk at 4pm and expecting it back by 9am isn’t really respectful.”
What is your current Lean passion, project, or initiative?
I’m trying to figure out how to expand on the ideas I introduced in A Factory of One. How do you take these lean concepts and apply them to teams? How can you improve the coordination and efficiency of the workflow of a group of people? I think that Agile methods from the software world point the way, because there’s not much difference between developing a piece of software development and, say, developing a marketing plan. Both involve multiple people sharing information and coordinating their efforts. That’s an area I want to dig into more deeply.

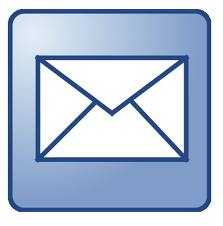





A Factory of One was work-life changing for me. The two biggest challenges I face today is how people view and manage their own work, which Dan's book addresses perfectly, and then how teams could and should work in a more lean way to produce more that's value-adding within shorter time frames. I very much look forward to whatever he comes with on improving teams this way.
ReplyDeleteDan wrote an excellent book for applying lean to our personal lives. He gives us a way to add value and enrich our daily activities. I too am looking forward to his next work.
ReplyDelete