As a customer, you know how you feel when a supplier lets you down by giving you poor service or by failing to deliver the right quantity and quality product at the right time. When the shoe is on the other foot and you are the supplier we see it different. These situations usually mean that your system has broken down and you need to initiate some form of corrective action, rework, to try to recover the situation.
Nearly
every business has some level of ongoing rework. Most product-based businesses
have some form of rework when they don’t satisfy the customer with their first
effort. It may be that you can’t supply the complete order in one lot, or the
quality of the product does not meet the customers’ needs. In service businesses,
rework can occur when the customer is not happy with the service and some form
of corrective work or follow up is required by the management team.
Scrap
and rework costs are a manufacturing reality impacting organizations across all
industries and product lines. No matter why scrap and rework occurs, its impact
on an organization is always the same—wasted time and money. Activities that
reduce the quality or efficiency of a manufacturing operation or business
process, but are not initially known to managers or others seeking to improve
the process are referred to as “The Hidden Factory.” Most organizations have
some form of a Hidden Factory.
Often,
the corrective work occurs so frequently that the management team accepts
rework as a normal part of business. This is a very dangerous interpretation of
rework as it can hide many problems that should be made to stand out. A close
examination of each and every cause for rework can provide improvement
opportunities that can really lift business performance.
Instead
of trying to fix the rework process (which is Muda), determine the root causes
of needing rework/repair and fix those. If priority is given to evaluating and
improving your manufacturing processes, it becomes much easier to reduce the
amount of scrap and rework in your organization. Remember, Lean is about zero
defects.
The
first step to understand the size of your rework problem is to set up a
monitoring system that will capture the data, including what happened and the
reasons why. Building a system to record each individual rework event will
establish baseline data that will enable you to assess future progress as your
team works to eliminate rework. This
data is also valuable as you can use it to start to understand just how much
money is being consumed by the rework process.
It is often surprising to realize the total cost of the hidden factory,
but this can provide the strong motivation to attack the causes of rework.
To
maintain a competitive edge, manufacturers must constantly find ways to cut
costs and improve efficiency. One way companies can save time and money is by
preventing scrap and rework. Correcting your systems by finding and eliminating
the root causes of rework will result in a much smoother workflow where good
days become normal.

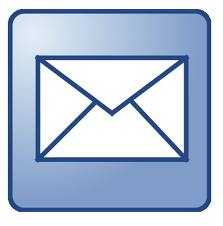





Hi Tim. Once the data is collected, and you've got the relevant cross parties (the ones contributing to your rework problem) together in a room, what's your advice as to the APPROACH to take when they're all together
ReplyDelete