Unfortunately, there are not enough organizations that understand quality. Quality is not additive or final. It must go beyond the product or service. We cannot add it at the end of the line or inspect it into the product. At best that is only a false sense of security. If we want a quality product it must be made with quality processes by quality minded people.
Inspection
can be useful to gather data on the process. Using that data to see if a
process has gone out of control and a special cause needs to be investigated is
useful. Using that data to evaluate the success, or failure, of an attempt to
improve (via the PDSA cycle) is useful.
Many
traditional companies use a final inspection department to 100% check the
product just before it is shipped to make sure that any errors that occurred
in-process are caught before the product is shipped.
Inspecting
to pull out the failed items from the production before a customer sees them is
a path to failure. When companies do this, they are trying to inspect quality
into the product. However, 100%
inspection has been shown to be only about 80% to 85% effective. If the process
is this bad, the process needs to be improved.
"Inspection
does not improve the quality, nor guarantee quality. Inspection is too late.
The quality, good or bad, is already in the product. As Harold F. Dodge said,
“You can not inspect quality into a product." — W. Edwards Deming, Out of
Crisis, Page 29
In
some organizations, we might as well give the quality folks a uniform, a badge
and a gun. They act like they are the Quality Police. Progressive companies
realize you cannot inspect quality into a product. By the time product is inspected, its level
of quality has already been established. The primary means of ensuring a
quality product is delivered is not by waiting until the product is assembled
to test it. Great companies build quality in from the start and maintain that
quality throughout the manufacturing process. To improve quality, you have to
improve the process that produced it.
Generally
the most effective way to achieve quality is to avoid having defects in the
first place. It is much less costly to prevent a problem from ever happening
than it is to find and correct the problem after it has occurred. Focusing on
prevention activities whose purpose is to reduce the number of defects is
better. Companies employ many techniques to prevent defects for example
statistical process control, quality engineering, training, and a variety of
tools from the Lean and Six Sigma tool kit.
Start
with the idea of preventing defects, not waiting until they are identified and
correcting them. Many companies have an active Zero Defects policy where defect
prevention is paramount and quality inspection is almost just a verification of
what they already know – that the product is defect free. If we can start with
quality and maintain that quality throughout the process we will have a quality
product.
Quality
is about prevention—you cannot "inspect" quality into a product. It
has to happen before the inspection process.

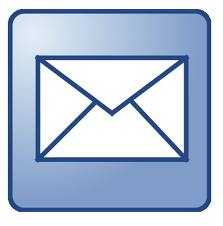





Hi Tim
ReplyDeleteBusiness that use final inspection to catch defects, generally drive up their rework and scrap costs. If you stop and fix an issue as soon as it comes up, at worst you lose one unit of production or you have one unit that needs some extra work. But if you choose to ignore it you can scrap or rework hundreds if not thousands of units. It is still common in some companies that they keep running despite an issue arising. One such company routinely has to fix several hundred units, because they ignore issues until after production is done for the day or even at times the week, while one of their competitors will stop a line to fix an issue right away. It may surprise some people, but one company is always struggling and their quality focussed competitor is healthy and growing steadily.