Here are the most common pitfalls in process mapping and some possible remedies:
- "Unbalanced" map (too much detail in some areas, not enough in others).
Remedy: Compare to other parts of the map; ask, "Does this step contain roughly the same amount of effort as that step?" - Gaps (missing or uncertain steps).
Remedy: Ensure that those who help create the map are knowledgeable of the process, or hav others review the draft for completeness and accuracy. - Map too "busy."
Remedy: Use additional paper and plenty of white space, or expanded maps cross-referenced to base map. - Takes too long, or people get bogged down.
Remedy: Establish ground rules:
- outstanding items list
- move on after 5 minutes
- follow rough draft principle; first get it down, then get it good
- use a facilitator. - Unclear terminology, or cannot remember what was said about a particular step.
Remedy: Take notes while mapping, create a glossary of terms. - Group is mixed or defers to designated decision makers.
Remedy: Stress that firsthand knowledge of the work process is what matters. Strive for equal participation, even if it means redefining the group. Try to prevent this problem by staffing the group with the right mix up front and explaining to management that they should select those closest to the work.

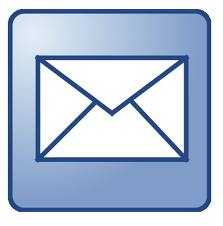





Bruce Hamilton gave a webinar presentation awhile back called Value Stream Mapping Mistakes & Faux Pas. A few standouts: Conference Room VSM equals no new learning and no credibility on the shop floor; working on assumptions with no idea if right or wrong. If you've got "50 Yards of Brown Paper" on the wall, you've got too much head-spinning detail and a poor visual representation (the opposite of effective A3 Thinking). Going to Gemba useless if you don't look and listen (if you think you already have all the answers, there is a fundamental problem in embarking on the exercise in the first place). Ultimate takeaway: You can't learn to see if you don't look.
ReplyDelete