Lean thinking is a great business system, but its approach requires support and commitment for organizations. Lean provides a framework to improve the flow of a process, it is therefore important to create a plan or roadmap describing the improved flow, highlighting changes, and areas for improvement.
Roadmaps are handy little
things, helping to point the direction while on a journey. Sometimes they serve to identify markers on
the road letting us know how far along we are, or telling us how far to go to
the next marker.
There are 5
steps for creating a Lean implementation roadmap for your journey:
1.
Vision,
Goals, and Objectives
The first place
to start this process is with the senior leadership. What is our vision for the
organization in the next few years? What are the biggest issues facing the
organization today that prevent us from achieving this vision? Define the
organization's true north - the business needs that must be achieved. These
will exhibit a magnetic pull for the organization, the same way a compass
guides the traveler. If we don't know where we are going, we'll never get
there!
An air of
excitement exists where people see real change occurring and can envision the
potential for future improvement. It’s time to align the entire organization
around our strategy and ensure we are all pulling on the same rope.
Departmental objectives need to align with the company purpose and vision for
the future.
2.
Proposed
Lean Framework
There are many
Lean strategies/frameworks/models available to reduce non-value adding
activities. It is necessary to develop a systematic methodology and analytical
model to select appropriate Lean strategies taking into account the
manufacturer’s focus on improvement areas (wastes), within their particular
resource constraints. By selecting appropriate Lean strategies, a manufacturer
can better prioritize implementation efforts and resources to maximize the
benefits of implementing lean strategies in their organization.
3.
Lean
Self-Assessment
Evaluating the
Lean practice in different areas provides a baseline for the organization. A
lean assessment is intended to examine an organization’s systems, behaviors,
and culture, and in doing so identify strengths, opportunities for improvement,
and the critical gaps that slow or inhibit a lean transformation. The assessment
provides an overall index of lean performance score of an organization.
Understanding the lean index can contribute to successful lean implementation
as it provides authentic results for lean performance and directs
decision-makers to corrective actions. It is important to perform an assessment
by an experienced team. The lean implementation team might have the necessary
experience, but external consultant might be required to provide an additional
beneficial perspective in the planning stage.
4.
Training
Plan & Resources
Identify training
programs for the employees and managers on Lean knowledge. The resistance to
lean transformation among managers is usually caused by the lack of skills and
lean knowledge. Likewise, employees’ resistance to lean improvements is likely
due to inadequate training and commitment. To overcome these problems, the organizations
should emphasize effective lean-related education and training programs as well
as establish training assessment to measure the training impacts.
The most effective
way to resource a Lean transformation is through a combination of developing
internal resources and providing external support from experienced Lean
coaches. Developing the internal lean specialists means that your organization
will gain the skills to sustain the change and to keep improving. Complementing
these individuals with external resources does a number of things. It provides
you with the know how in Lean and the experience in leading a Lean
transformation. The Lean coach will have experience in change management and
should be able to clearly identify the cultural and leadership barriers to change
within your organization. They should help you develop strategies to overcome
these barriers.
5.
Monitor
and Adjust
Now that the
organization strategy is aligned and resources are deployed on what's
important, we must monitor the results of our activities and make corrections
based on results. Put the Plan-Do-Check-Adjust continuous improvement cycle to
work.
All the business
excellence models across the globe are built on achieving a continual
improvement in all dimensions of the business. Excellence is a paradigm in which
the organizations strive to excel others initially and over a period of time –
develop a culture of excelling themselves. Lean thinking drives the
organizations to excelling themselves regularly.
A Lean roadmap
provides a systematic implementation process: specific actions in order of precedence
that are milestones in the journey from mass to Lean production. A Lean roadmap
is not a cookbook of actions that must be strictly followed for every
implementation because every implementation will be singular, in that every
company has its own culture, and inheritance policies and systems, which will
either support or delay the Lean journey.

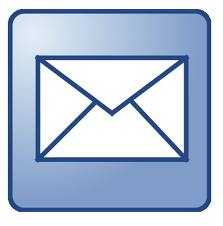





No comments:
Post a Comment