The manufacturing process is not the only area of a company that incurs waste on a regular basis. Although most of us focus on the factory floor to identify the improvements needed to increase our competitiveness, many companies find abundant opportunities for waste reduction in the office.
In the office environment, the 8 classic waste types of the Lean methodology manifest in different ways than we see on the factory floor. Here is a list of the 8 wastes of Lean, and some ideas about how they manifest in the office environment.
Transportation = movement of the work. Manifestations include handoffs where the work is transferred from one person to another. Transportation of electronic files is particularly insidious because it frequently results in multiple, varying copies of the work, which must eventually be reconciled. It leads to other wastes such as defects, overproduction, and processing. Transportation is also an opportunity for a defect when the work goes to the wrong person or fails to get to the right person.
Inventory = work that is waiting to be processed. Inventory is a common result of multi-tasking and otherwise un-balanced workloads. Inventory can be found in e-mail or work order in-boxes, to-do lists, product development pipelines, and resource assignment charts. If a person has three tasks to complete, it is guaranteed that two of them are waiting (in inventory) while that person performs the third. If you want to be able to see inventory like you do on the factory floor, you must make the lists, in-boxes, resource assignments, and project pipelines visible in your workspace.
Motion = people moving or working without producing. Meetings are motion in the sense that they are work without producing, unless a decision is made or information is produced during the meeting. The motion you see of people moving from conference room to conference room and back to their desks is indeed wasted motion, but it’s probably not the waste to target first. Motion shows up as people search for files they can’t find, in phone calls to track down information, or from unnecessary button clicks to get to the bottom of a work order to update the to-do list. Most un-productive work takes place inside the electronic system while the person is sitting at his/her desk or while they are sitting in a meeting.
Waiting = people waiting for information in order to do work. This is another common result of multi-tasking, and also the primary cause of multi-tasking. People work on other things while they wait for one thing to be processed and made ready. Unfortunately, when the one thing finally becomes ready, we tend to finish what we started before getting back to it. Because of multi-tasking, waiting is difficult to observe. You must ask questions to discover it, or identify it yourself when you run into it. It’s perhaps the most common and wasteful waste of them all in the office.
Overproduction = producing unnecessary work or deliverables. Overproduction shows up in multiple copies of information, producing reports that aren’t read, writing formal documents or content where only the table is read, reply all, working on deliverables that aren’t important, and delivering the same information in multiple deliverables or formats. Overproduction frequently shows up when managers ask underlings to do things that make the manager’s life easier.
Over Processing = unnecessary effort to get the work done. Over Processing shows up in additional signature approvals, data entry or data format changes, frequently revising documents or information, or complex forms or databases that require information to be entered repeatedly. Over Processing often results from the creation of multiple versions of a piece of work, that now must be reconciled into the true work.
Defects = any work that did not accomplish its purpose or was not correct the first time. Defects include late work, incorrect information, conflicting information, instructions that must be clarified, insufficient information, partially complete work or information, miss-named files, lost files or information, and anything that must be reworked. Rework is the pain that results from defects. Find the re-work and you will find the Defect waste.
Underutilized Skills, Ideas = capabilities of people that are not used or leveraged. This happens frequently in large organizations where the skills and backgrounds of everyone are not common knowledge. This can vary from not capturing ideas that employees might have for new products or innovations, to the six-figure salary executive correcting data entry errors in a financial spreadsheet. The biggest crime in this category is not empowering or enabling the people most intimate with a process to improve the process.
Transferring Lean manufacturing concepts to the office may take some convincing. First, office employees must accept the philosophy as appropriate for their work space. Individuals may find it hard to imagine implementing concepts originally designed for factories into a working office environment. While they wade through company policy, orders and emails, the factory folks are already steeped in the language of Lean and comfortable with words like “kaizen” and “kanban.” Once office employees increase their confidence level with the Lean concepts, they’ll want to share improvements and ideas with their shop floor counterparts, bridging the gap between the shop and the office, and increasing loyalty, enthusiasm and pride within your company.

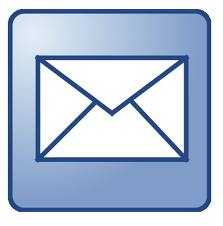





Great explanations. It is often hard for employees to see waste in a transactional environment. I really like your examples.
ReplyDeleteGreat breakdown. I think it's more than reasonable to push for these kinds of efficiencies in the office environment. Nice work!
ReplyDeleteTerrific article, Tim. You rock!
ReplyDeleteI work for a chemical plant. What I feel hard to reduce of 7 waste from my workplace is excess motion.
ReplyDeleteThe other problem is over processing. Many non-value added processes are done in my workplace. And I try to reduce it.
Bringing the 8 wastes from the manufacturing floor to the office is a great idea. The more people are educated on its ideology and benefits, and the more comfortable people are with lean ideology, the more widespread the improvements will be.
ReplyDeleteHi Tim, this is a great explanation of the Lean methodology’s 8 wastes and how they manifest in office environments. Addressing inefficiencies beyond the factory floor is vital. Making these invisible wastes visible, such as by mapping inbox backlogs or identifying overproduction in redundant reports, is important for identifying areas that need improvement. This article also explains the challenge of transferring Lean principles to office settings very well. Particularly the cultural and mindset shifts required for non-factory workers to embrace these practices. Encouraging collaboration between office and factory teams to share Lean improvements is an excellent suggestion to foster a cohesive company culture.
ReplyDelete