Organizations
generally adopt Lean to move the needle on specific indicators. They want to be
more productive, improve the health of the organization, or increase revenue.
But the Lean
concept isn’t simply about improving metrics; it is about changing the culture.
And changing the culture begins with leadership. Everyone from the top down
needs to begin re-framing the work, enacting the values, and striving for
perfection.
Lean production
can only be achieved if the performance of the workers involved are at its
highest level. Lean managers, however, must not forget that organizational
performance always comes down to the behavior of the workers, which are always
determined, by competence and motivation.
Therefore, Lean
managers are also tasked to motivate their employees in order for them to
internalize the organizational goals and the individual goals of each work
unit. Lean leadership is about mentoring, embodying, and inspiring Lean
thinking and Lean values throughout your organization.
The following 5
techniques are used by Lean managers to build a motivational culture in the
organization.
1. Sense of
achievement
Management must
create among workers the feeling that they achieve something, both individually
and collectively. Recognition must be given for both individual and group
achievement. Management must make sure that workers feel that sense of
achievement whenever a goal has been reached or when new innovations have been
effected. Show team achievements during stand-ups meeting in the morning.
2. Learning and
growth
Learning and
growing within an organization is a continuous process. It does not end when a
worker has mastered the necessary skills of his job. Management must give
workers opportunities to learn new skills to enable them to move to different
level, possibly a higher one, within the organization. Further education and
training opportunities must be made available to workers who have ambition to
grow in the organizational hierarchy. Try to organize small training sessions
where people share field experience and tips.
3. Stimulating
work
Management must
create a work environment that will be stimulating to the workers. Continuous improvement culture must stimulate workers to solve small problems, to spot
waste, to collaborate and feel responsible for all the achievements of the
organization and for the clients.
4.
Responsibility and empowerment
Workers are
given their individual and collective responsibilities as an individual worker
and as a member of the team. Together with the responsibility given comes the
empowerment of the same. Workers must be empowered, or given the authority, to
carry out their responsibilities.
5. Feeling of
being part of something
A worker must
never feel that is just one of the many nameless and faceless workers in the
organization. He must be given recognition as a contributor to the achievements
of the organization. Every single worker must feel that he is part of something
important in the organization. He must feel that he is an important cog in the
organizational machine.
Lean thinking
starts at the top, but also from the inside out. Leaders must cultivate an
attitude of respect for others and humility within themselves. They use
questions and mentoring to lead employees to discover and enact their own
improvements, and support their decisions.
They serve
employees by removing obstacles and promoting flow. Over time, these behaviors
become learned and practiced by everyone on the team and everyone in the
organization.
Lean systems
are powerful ways to improve productivity, quality, and profits. But they
cannot be simply adopted as quick fixes to target certain metrics; they must be
fully adopted, committed to, and practiced daily by everyone in the
organization.
A leader has
the opportunity to inspire and foster these behaviors or undermine them.
Adopting continuous improvement within yourself is the first step.

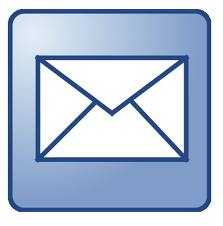





No comments:
Post a Comment