There is no
room for compromise in Lean when it comes to quality. We have to learn to build
quality into our processes and design Lean processes based on right-first-time
principles.
Building
quality into our processes means not simply relying on perfectly trained
individuals and teams who never make mistakes. Standard Operating Procedures
may help people making errors, but it does not stop them.
We have to
assume, just like in Murphy’s Law – that anything that can go wrong will go
wrong … eventually. And by accepting this fact, the most important aspect of
our processes is how well we design them to eliminate any potential errors from
ever occurring.
Lean is about
stopping and fixing issues when they go wrong: quickly and consistently, every
time. It is about creating the proper workplace setup, to ensure that when
things go wrong, we can identify them quickly.
Jidoka is an
integral part of Lean principles that focuses on optimizing the flow of
production processes. It plays a crucial role in helping organizations become
more efficient and productive by reducing waste, enhancing quality, and
increasing customer satisfaction. Jidoka is based on the idea that any defect
should be detected immediately so the process can be stopped until the root
cause of the problem is identified and corrected. This helps eliminate wasted
time, resources, and energy from running defective parts through a production
line.
The
implementation of Jidoka relies on a mix of cultural concepts and Lean tools
that are summarized below.
Developing a
Jidoka mindset. Many
people are trained to react to problems and to put in place quick fixes. The
concept is to keep things running for as long as possible and work around
problems as quickly as possible. A Jidoka mindset is different in that it says
that, in the long run, efficiency will come from addressing the root cause of
problems and that investing time in solving problems is a valuable investment.
Empowering
staff to ‘stop the line’. Do
your staff feel that they are empowered to say ‘stop’ when they see an unsafe
act or a problem occurring? Many organizational cultures, through the words and
actions of managers, disempower staff from stopping a process. Developing a
culture where people feel that they are able to raise a real issue – and that
far from being penalized they will actually be thanked for raising the issue –
is very important in jidoka.
Installing
andons. Andons are
audible, or more commonly visual, signals that something has happened.
The aim is that andons quickly alert managerial and technical staff to a
problem having arisen so that they can get to the source of the problem and
begin to investigate it.
Solving the
root cause. Quick
fixes are typically just that. Jidoka relies on the implementation of an
immediate fix to stem the potential damage and on the longer-term fix that
comes through root cause analysis.
Utilizing
standard work. Having
implemented the changes it is vital to document what has been done and to carry
out any training required on the new process.
Selective
automation. Selective
automation is about investing in technology to detect – and more ideally
prevent – errors arising wherever there is a business case to do so. This means
wherever there is either a high probability that things will repeatedly go
wrong, or where a problem arising has significant impact (such as the ability
to cause harm), then it means investing in sensors and other systems to enable
you to control the process and detect problems as early as possible.
By not fixing
the problem as soon as it is identified increases the costs of fixing it later.
It potentially allows the problem to get to the customer and kills causing even
more damage to the business. And really importantly, in a culture of continuous
improvement, we want to learn fast.
If the issue is
not addressed immediately, we miss the opportunity to learn (kaizen) and when
we finally do get around to fixing the issue, we might find we don’t just have
one product that has failed but multiple products.
The sooner the
problem is detected, the easier it is to fix and the smaller the impact. Thus, one of the important parts of Lean is
to be able to detect problems, raise them quickly, analyze and fix.

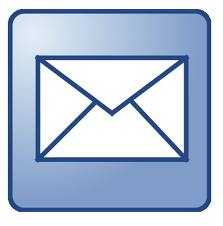





No comments:
Post a Comment