"Still the question recurs “can we do better?” The dogmas of the quiet past are inadequate to the storm present. The occasion is piled high with difficulty, and we must rise with the occasion. As our case is new, we must think anew, and act anew." — President Abraham Lincoln in his Annual Address to Congress (December 1, 1862)
Lean Leaders and Lean Thinkers should rally around this great quote from a great President. Can we do better? The answer was “YES!” which President Lincoln made clear as he exhorted all who would listen to think anew and act anew.
The answer was yes during the Civil War years and it is yes at your work site today. The harder question is “how?” How will you think and act anew? Do you need to think anew about an old issue that has been causing waste at your site? Do you need to think anew about how to make your process even better? Do you need to think anew about your problem solving methodology? Does your organization need to think anew and act anew by embarking on the Lean Journey?
Many organizations have been on the Lean Journey for some time. Many others are just starting or have not yet started. All need to think anew and act anew.
Today's Lean Quote is courtesy of my friend Christian Paulsen. Christian is an Executive Consultant with 20 years of Lean Manufacturing. Chris adds value to organizations by driving process improvement and bottom line savings. Chris intends to help others by sharing the lessons learned after a quarter century of operational leadership, marriage, parenting, and even longer as a Cubs fan. He blogs at Lean Leadership and can be found on Twitter as http://twitter.com/chris_paulsen.

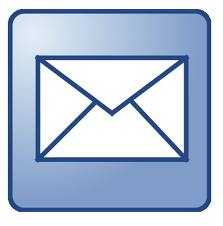




