Feel free to share some of your favorites here as well.
“Do not look where you fell, but where you slipped.” - African proverb
This quote really gets to the essence of root cause analysis. Where do you focus your attention; on the slippery floor or what caused the floor to get slippery in the first place.
Root cause analysis is a problem solving methodology based on the belief that problems are best solved by attempting to correct or eliminate root causes, as opposed to merely addressing the immediately obvious symptoms. By directing corrective measures at root causes, it is hoped that the likelihood of problem recurrence will be minimized. However, it is recognized that complete prevention of recurrence by a single intervention is not always possible. Thus, root cause analysis is often considered to be an iterative process, and is frequently viewed as a tool of continuous improvement.
Mark Graban of a leanblog.org has created a photolog called BeMoreCareful.com. This is a collection of workplace signs and posters that don't quite get to the root cause. The site intended to show pictures of workplace signs that say things like:
Caution!
Warning!
Be Careful!
LOOK OUT!
Don’t Forget!
These signs usually have an exclamation point and often say “Please.” Signs and warnings are about the weakest form of “error proofing,” if you can even call it that. Some find it easier to just slap up a sign, thinking the problem is solved, instead of looking for a more systemic fix. Lean thinking recognizes that people are human and that human error is inevitable. Instead of posting a sign Lean focuses on the process so that it’s more difficult for people to make mistakes or forget things.
Here is an example of such a sign:
Before printing, check the printer for signs! Chances are, you’ve already hit “Print” before walking over to see this caution. Is there a deeper root cause to the “28lb Type 2 error”? See more examples at BeMoreCareful.com.
Disclosure: I am a contributor on the photolog BeMoreCareful.com.

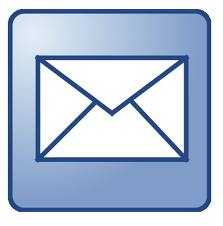




