In manufacturing processes small amounts of wasted motion can add up quickly over the course of an entire production run. This video from Assembly Services and Packaging illustrates how optimizing your production line can affect the bottom line.

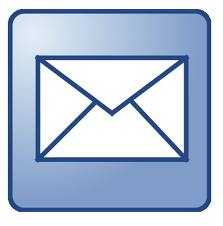





The challenge is about getting rid of one object a day, for … a month? A year? It’s up to you how long you want your challenge to last.
Whether you give away, trash or donate the object is immaterial, but it must be gone from your life and space. Putting it into storage doesn’t count; though you are allowed to, say, collect the things in a box to donate them at the end of the month.
Oh, and you’re also allowed to cheat and fill your quota ahead of time, like throwing out 7 things on Monday, making that a week’s worth of ATAD.
By telling us on here what you got rid of today will not only help with the accountability issues, you’ll also help others rethink their possessions (He got rid of his xyz? Come to think of it, do I really need mine?)
all of the activities that move materials and information from suppliers to end customers: planning, sourcing, transporting, manufacturing, inspecting, sorting, packing, and consuming, as well as managing the entire process.The total cost of fulfillment is all of the costs of moving material from one end of the fulfillment stream to the other.
These go far beyond the transportation costs most firms calculate to include the carrying and storage costs of inventory, the cost of material handling equipment and labor, and the management time devoted to gathering all of the information needed to constantly monitor performance. These costs also include all of the transport, inventory, handling, and management costs incurred by customers and suppliers along the fulfillment stream.The authors list eight guiding principles for creating lean fulfillment streams:
1. Eliminate all the waste in the fulfillment stream so that only value remains.The process of understanding and improving the fulfillment stream follows the same process of value stream mapping. The current state data includes total lead time, inventory (average days on hand), inventory carrying costs, and perfect-order execution. The execution of a perfect order is characterized by “8 Rights”:
2. Make customer consumption visible to all members of the fulfillment stream.
3. Reduce lead time.
4. Create level flow.
5. Use pull systems.
6. Increase velocity and reduce variation.
7. Collaborate and use process discipline.
8. Focus on total cost of fulfillment.
Right quantityThe future state vision must include a plan for these 6 areas of the fulfillment stream:
Right product
Right place
Right time
Right quality
Right source
Right price
Right service
Customer collaborationThe authors stress collaboration across all functions and firms as the way to minimize the total cost of fulfillment. They use about half the book to describe actions that can be taken in the 6 areas to minimize waste in the fulfillment stream. There is a stronger emphasis on total cost of the fulfillment stream rather than customer value. While they list the steps for improvement there is very little discussion about how to engage those parties in the fulfillment stream for such a successful collaboration.
Outbound logistics
Shipping, receiving, and trailer-year management
Material ordering
Inbound logistics
Supplier collaboration