I am a proud participant of the Western Massachusetts Lean Network. This is a network of Lean thinkers at various stages of their journey whose goal is to share best practices within the network as a way for all of us to continue learning. The Greater Boston Manufacturing Partnership (GBMP) is the host of our network. We recently started a forum for sharing online where we can post a question of the week.
I suggested the following question a couple weeks ago:
What are your thoughts on Lean in the office compared to Lean in a production setting?
I suggested the following question a couple weeks ago:
Does it seem more difficult to do administrative kaizen then production/operations kaizen? If so, why?Bruce Hamilton, President of GBMP and Vice Chair of Shingo Prize (aka Mr. Toast), gave an insightful response.
In responding to this question, the following comment from Shigeo Shingo comes to mind: "The real problem is thinking there is no problem." Having spent half of my career in administrative functions (marketing, IT, materials management), I'm well aware that there are loads of problems in the office environment. Information wells, disconnects, and mazes are normal as are correction loops. Office layouts create huge excess motion and encourage batching of everything from sales leads to factory and purchase orders to inspections to invoices – and finally collections. Every piece of information is batched with all the problems that attend that practice. (Of course there are occasional exceptions to this stereotype, so before continuing, I apologize to them.)My experience with Lean in the office mirrors that to which Bruce summarized. Lean is a building, thinking process which requires both learning and thinking by building on experiments. Bruce provides some logically first steps for any kind of improvement activity.
The barrier to engaging administrative departments is initially higher than in production for are several reasons:
• Top management is predisposed to round up the usual suspects when problems occur, and those suspects are in production. Management rationalizes that problems occur there because production employees are less well formally educated or because they are paid less and are therefore less likely to care about their work – or maybe they're tired from working a second job and therefore more prone to mistakes. None of this is true, of course, but production often faces this bias and then takes it on the chin when problems occur.
• Office employees take their lead from management and tend to have the same misconceptions about production. At the same time they have an unchallenged complacency for their own situations. While production has a long history of absorbing blame, office employees have remained mostly above the fray when problems occurred.
• Knowledge work" as it's called is not so visible and is mostly unscrutinized. Although waste in knowledge work is huge, office employees fly below the L,M&O radar.
• Office employees (including department managers) have more position power than factory employees and are therefore better equipped to fight change. Many a change agent has been derailed by choosing to battle a savvy office manager.
• Managers of administrative functions are often paid commensurate with the number of reports, so a system that may recommend few reports will not be motivating.
The challenge to overcoming these initial barriers is to:
1. First identify early victories that make the job "easier, better, faster and cheaper" (the theme of our October 19-20 Northeast Shingo Conference). Don't pick a project that involves work or them with benefit only to production (e.g. "Scheduling smaller batches" or "More timely and accurate forecasts.") Pick projects lessens their loads (e.g., "easier pricing system for order entry" or "better customer information for collections" or "printers in the right locations.")
2. Choose "small" projects that can be completed quickly and make sure resources (often IT) are available to complete the efforts.
3. Third, publicize victories to the stakeholders keeping in mind all of the objections and predispositions (and surrounding politics) implied in the points above. Share the success and give credit to managers and employees. Provide explicit descriptions of before and after conditions with hard numbers.
The bottom line is that administrative departments will buy-in once managers and employees understand the benefits and are persuaded that these far outweigh any potential threats. Your objective is to respect and answer their objections while they are learning.
What are your thoughts on Lean in the office compared to Lean in a production setting?

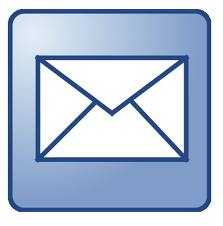




