A
reader recently asked me how to promote a common skill base for communication
in regards to a Daily Lean Tip. Proper communication in the workplace is
essential so I thought I would share my thoughts here with everyone.
In
today's team-oriented workplace, the development of good interpersonal
communication skills is an important key to success. With a bit of practice
and some instruction, you can be on your way to building positive communication
skills to use in your workplace and beyond.
The
process of communication involves establishing a link with another person
either directly (verbal or non-verbal) or indirectly.
Basic
Communication Principles include:
- Communication is an exchange of
information
- Communication is always and only
one to one
- There are two processes when
communicating – sending and receiving
- As a sender, we can use tools and
skills to LINK with another person
- As a receiver, we can use tools
and skills to understand what is being conveyed
- Information can be exchanged
directly through words (verbal) or emotions (non-verbal)
- Information can be exchanged
indirectly through posters, signs, videos, e-mail or voice mail
The
attitudes you bring to communication will have a huge impact on the way you
compose yourself and interact with others. Choose to be honest, patient,
optimistic, sincere, respectful, and accepting of others. Be sensitive to other
people's feelings, and believe in others' competence. Good communication must
be H.O.T.
H.O.T.
stands for honest, open, and two-way.
Communication
is a key ingredient for empowerment. Give every employee equal and direct
access to information. Many companies have developed a trickle-down style of
communication that alienates those employees who may not be "in the
loop." The more informed employees are and the more communication is open,
honest, direct and complete, the more likely employees are to feel empowered
and connected to the daily operations and overall goals of their company.
Open
communication is at the center of Lean and Respect for People. Employees need
to know what is expected of them and how they’re performing. Visual displays
such as scoreboards, scheduling charts, team communication boards, and
recognition displays all help to keep information flowing between employees,
departments and upper management.
Communication
is the glue that binds an organization together but do not assume that several
announcements and a note on the notice board is sufficient to get the story
out. Some say to communicate seven times and seven ways but that does not mean
seven months apart. Develop and implement a robust communication plan and check
to see if the total target audience has received the unfiltered message. If you
want to know if your message is getting out clearly why not ask the most obscure
person on the night shift if he or she heard the message? The day shift is easy
but how about the rest of the folks?
To
be an effective communicator remember The “Be List”.
- Be A Teacher
- Be Enthusiastic
- Be Positive
- Be Consistent
- Be Demanding but Considerate
- Be Courteous
Not
only should one be able to speak effectively, one must listen to the other person's
words and engage in communication on what the other person is speaking about.
Avoid the impulse to listen only for the end of their sentence so that you can
blurt out the ideas or memories your mind while the other person is speaking.
Effective
communication is all about conveying your messages to other people clearly and
unambiguously. It's also about receiving information that others are sending to
you, with as little distortion as possible. Doing this involves effort from
both the sender of the message and the receiver.
Developing
advanced communication skills begins with simple interactions. Communication
skills can be practiced every day in settings that range from the social to the
professional. New skills take time to refine, but each time you use your
communication skills, you open yourself to opportunities and future
partnerships.

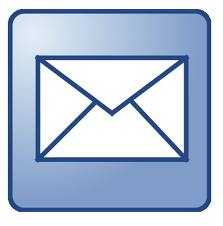




