In
this month’s ASQ post Paul Borawski asks about quality beyond it’s roots in manufacturing.
Customers
and companies alike recognize that quality is an important attribute in
products and services. Suppliers recognize that quality can be an important
differentiator between their own offerings and those of competitors.
It
was in the second part of the twentieth century that ‘quality’ boomed in
application by industrial and service organizations. Japan and the United
States were the first countries to look at quality as an important competitive
advantage. However, the quality movement can trace its roots back to medieval
Europe, where craftsmen began organizing into unions called guilds in the late
13th century. Until the early 19th century, manufacturing in the industrialized
world tended to follow this craftsmanship model. The factory system, with its
emphasis on product inspection, started in Great Britain in the mid-1750s and
grew into the Industrial Revolution in the early 1800s. In the early twentieth
century, manufacturers began to include quality processes in production. It was
only in the late 1970s that service quality emerged as a solid management
discipline and practice.
Recently,
quality improvements (and Lean) have moved from manufacturing plants to
operations of all kinds, everywhere: insurance companies, hospitals, government
agencies, airlines, high-tech product development units, oil production
facilities, IT operations, retail buying groups, and publishing companies, to
name just a few. In each case the goal is to improve the organization’s
performance on the operating metrics that make a competitive difference, by
engaging employees in the process and improvement activities.
The
biggest challenges in adopting the quality (and Lean) approach in nonindustrial
environments are to know which of its tools or principles to use and how to
apply them effectively. Organizations succeed or fail based on what happens within
specific key business processes. Focused process improvement is a fundamental requirement
to sustain initiatives like quality or Lean and to generate positive results.
All
products and services are produced and delivered through work or business
processes. A process can be defined as the sequential integration of people,
materials, methods, and machines so as to produce value-added outputs for. A
process converts measurable inputs into measurable outputs through an organized
sequence of steps. Furthermore, the process model applies to both manufacturing
and nonmanufacturing work.
Nonmanufacturing
processes differ from their manufacturing counterparts in any of three ways.
Manufacturing is unique in that (1) its customers are isolated from production,
(2) its outputs are tangible, and (3) its operations are highly repetitive. By
contrast, customers usually are involved directly in the delivery of services,
and the value added by nonmanufacturing processes is often characterized as
intangible. Some nonmanufacturing processes are repeated infrequently, and
their outputs can be unique.
Customer
participation in the production of the output is the first key characteristic
which distinguishes manufacturing from nonmanufacturing processes.
Many
organizations don’t sustain their quality or Lean efforts
because they are not focused on improving critical business processes. Successful
companies recognize the need to extend the quest for quality beyond
manufacturing. Quality awareness must be inherent in all aspects of our
business through new product development, manufacturing, administration, sales
and customer service.
As
the quality (or Lean) approach percolates into ever wider circles, it ceases to
be about best practices and starts to become a part of the fabric of doing
business. The next level of the quality
(or Lean) journey is managing the softer side of the equation – less about
tools and frameworks, more about building the energy and engagement of
employees from the shop floor and the office, tapping into their ideas,
focusing them on constant problem solving, and keeping them open to change and
flexibility.

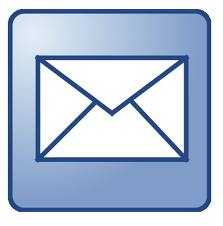




