Click this link for A Lean Journey's Facebook Page Notes Feed.
Here is the next addition of tips from the Facebook page:
Lean
Tip #1606 - Hire or Develop Lean Leaders and Develop a Succession System
The
key here is not to take ownership of the plan but to provide conditions in
which the team can implement Lean. The aim of this approach is to create a
nucleus of people who are trained in the Lean tools and techniques, who have
experienced Lean through hands-on application and who can then with some
external support move on to help others create lean processes by transferring
their knowledge.
Lean
Tip #1607 - Create a Positive Atmosphere
Be
tolerant towards mistakes committed in lean environment with a supportive and
learning attitude. Have patience with progress as this will be key to get
results and also try to create a blame free supportive environment. Have
courage to take risks at crucial stages to push things and resources to meet
the plan and achieve results.
Lean
Tip #1608 - Benchmark With Other Companies
Visit
other companies that have successfully implemented lean to get ideas and
understanding; other companies are often delighted to present their lean
implementation progress. Networking is key to ensure global understanding with
other companies implementing Lean.
Lean
Tip #1609 - Set up a Lean Enterprise Steering Team
This
team would be responsible to provide support in the planning, resourcing,
implementation, and follow-up accountability for implementation. The steering
team is often identical to the normal line management team. The internal
resources and external consultants would provide consulting support to the
team. This infrastructure would resolve inter-departmental issues.
Lean
Tip #1610 - Use Experts for Teaching and Getting Quick Results
The
word "sensei" is used in Japan with some reverence to refer to a
teacher who has mastered the subject. A company needs a sensei to provide
technical assistance and change management advice when it is trying something
for the first time to help facilitate the transformation, get quick results,
and keep the momentum building.
A
good teacher will not do it all for you. You need to get lean knowledge into
your company, either by hiring experts or by hiring outside experts as
consultants. To develop a lean learning enterprise you need to build internal
expertise—senior executives, improvement experts, and group leaders who believe
in the philosophy and will spread lean throughout the organization over time.
Lean
Tip #1611 - Complete Most Important Tasks First.
This
is the golden rule of time management. Each day, identify the two or three
tasks that are the most crucial to complete, and do those first.
Once
you’re done, the day has already been a success. You can move on to other
things, or you can let them wait until tomorrow. You’ve finished the essential.
Lean
Tip #1612 - Get An Early Start.
Nearly
all of us are plagued by the impulse to procrastinate. It seems so easy, and
you always manage to get it done eventually, so why not?
Take
it from a recovering chronic procrastinator — it’s so much nicer and less
stressful to get an earlier start on something. It isn’t that difficult either,
if you just decide firmly to do it.
Lean
Tip #1613 - Don’t Allow Unimportant Details to Drag You Down.
We
often allow projects to take much, much longer than they could by getting too
hung up on small details. I’m guilty of this. I’ve always been a perfectionist.
What
I’ve found, though, is that it is possible to push past the desire to
constantly examine what I’ve done so far. I’m much better off pressing onward,
getting the bulk completed, and revising things afterward.
Lean
Tip #1614 - Turn Key Tasks into Habits.
Writing
is a regular task for me. I have to write all the time — for work, my hockey
organization, my blog, etc. I probably write 5,000 – 7,000 words per week.
The
amount of writing I do may seem like a lot to most people, but it’s very
manageable for me, because it’s habitual. I’ve made it a point to write
something every day for a long time.
I
rarely break this routine. Because of this, my mind is in the habit of doing
the work of writing. It has become quite natural and enjoyable. Could you do
something similar?
Lean
Tip #1615 - Create Organizing Systems.
Being
organized saves tons of time, and you don’t have to be the most ultra-organized
person in the world either. Systems aren’t complicated to implement.
Create
a filing system for documents. Make sure all items have a place to be stored in
your dwelling. Unsubscribe from e-mail lists if you don’t want to receive their
content. Streamline, streamline, streamline.
Lean
Tip #1616 - Promote a Culture of Learning.
In
today’s fast-paced economy, if a business isn’t learning, it’s going to fall
behind. A business learns as its people learn. Communicate your expectations
that all employees should take the necessary steps to hone their skills and
stay on top of their professions or fields of work. Make sure you support those
efforts by providing the resources needed to accomplish this goal.
Lean
Tip #1617 - Stress Training as Investment.
The
reason training is often considered optional at many companies is because it is
thought of as an expense rather than an investment. While it’s true that
training can be costly up front, it’s a long-term investment in the growth and
development of your human resources.
Lean
Tip #1618 - Choose Quality Instructors and Materials.
As
you probably don’t have unlimited time or funds to execute an employee training
program, you should decide early on what the focus of your training program
should be. Determine what skills are most pertinent to address current or
future company needs or ones that will provide the biggest payback.
Who
you select to conduct the training will make a major difference in the success
of your efforts, whether it’s a professional educator or simply a knowledgeable
staff member. Having the right training materials is also important — after the
training is over, these materials become valuable resources for trainees.
Lean
Tip #1619 - Clarify the Connections of Training and Their Job.
Some
employees may feel that the training they’re receiving isn’t relevant to their
job. It’s important to help them understand the connection early on, so they
don’t view the training sessions as a waste of valuable time. Employees should
see the training as an important addition to their professional portfolios.
Award people with completion certificates at the end of the program.
Lean
Tip #1620 – Make Training Ongoing and Measure the Results.
Don’t
limit training solely to new employees. Organized, ongoing training programs
will maintain all employees’ skill levels, and continually motivate them to
grow and improve professionally.
Without
measurable results, it’s almost impossible to view training as anything but an
expense. Decide how you’re going to obtain an acceptable rate of return on your
investment. Determine what kind of growth or other measure is a reasonable
result of the training you provide. You’ll have an easier time budgeting funds
for future training if you can demonstrate concrete results.

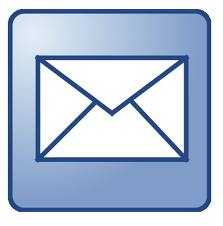



