Here is the next addition of tips from the Facebook page:
Lean Tips #2746 – Recognize What’s Going Well
Coaching well requires a balance of criticism and praise. If your coaching conversations are completely focused on what’s not working and what the employee has to do to change, that’s not motivating, it’s demoralizing.
Your recognition of the things your employee is doing well can be a springboard into how they can build from that to improve. Giving compliments that you don’t actually mean can have a worse effect than not giving any at all, so take the time to think about specific things that are going well, and let your employees know that you see and appreciate them!
Lean Tips #2747 – Listen and Empower
Coaching requires both encouragement and empowerment. As a manager and a leader, your job is to build one-on-one relationships with employees that result in improved performance.
Your employees are likely to have a lot of input, questions, and feedback. It’s important for them to know you care enough to listen to what they have to say, so encourage them to share their opinions.
Some employees will have no problem speaking their mind, while others will need a LOT of encouragement before they share an opinion with you openly. Once they do open up, be sure to respect those opinions by discussing them, rather than dismissing them.
Lean Tips #2748 – Understand their Perspective
When you’re coaching employees to improve performance and engagement, approaching things from their perspective, rather than your own, will help enormously with seeing the changes and results you want.
Everyone has different motivations, preferences, and personalities, so if you ask questions to help you understand where their “why” comes from and what their preferred “how” looks like, then you can tailor your coaching conversations to align the way they work best with the improvements you’re both aiming for.
Lean Tips #2749 – Coach in the Moment
If an employee comes to you with a question about a process or protocol, use this opportunity to teach them something new. If you’re not able to stop what you’re doing right away, schedule time with them as soon as possible to go over it.
Better yet, keep a weekly one-on-one meeting scheduled with each employee so you can go over questions and issues regularly, while maintaining productivity. Coaching employees with a goal of improving performance means making them a priority each week!
Lean Tips #2750 - Commit to Continuous Learning
Make a commitment to improve your own skills and competencies. If you’re not continuously learning, why should your employees? Lead by example and your team will follow.
Show that you are interested in their success (why wouldn’t you be?). Ask questions about where they see their career going, or how they see their role evolving in the company. Even if they don’t have a plan laid out yet, these questions will make them think about their career and what they want to accomplish within the organization.
Show your employees that you don’t just want them to do better so you look better, but that you’re actively interested in their career, accomplishments, and professional success.
Lean Tip #2751 – Focus on Gradual Small Changes Instead of Major Shifts
My advice is to focus on small gradual changes rather than large changes. Small changes can be made quickly, on a daily-basis, and are typically inexpensive. By focusing on small changes, you can remove barriers from just starting a continuous improvement process. This focus will allow your team to reap the benefits of their “small wins” right away. As more and more small changes are applied, your team will see an accumulation of benefits from them. This will give them more confidence to suggest more ideas.
Lean Tip #2752 – Prioritize Ideas that are Inexpensive
By going after the ideas that do not require a large amount of investment, you can remove the financial barriers of your continuous improvement efforts. This process can empower the line worker to suggest and implement ideas that can improve their working process because they know that their changes do not need upper management approval. Some ideas such as reducing waste, eliminating unnecessary steps, and re-organizing in the work processes fall into this category.
Lean Tip #2753 – Gather Ideas From the People Doing the Work
In a Lean and continuous improvement organization employees are your greatest asset and should also be the source of generating new ideas for improvement. No one knows the work better than the person who performs it everyday. No one has more “skin in the game” about the working process than that person. As a result, the best person to suggest ideas for improvement and to implement them is the line worker.
Lean Tip #2754 – Empower Employees for Improvement
Although employees play a vital part in the continuous improvement process, it is management’s role to train and empower them. Most workers are unaware of Lean principles and practices such as 5S, the 8 wastes, value stream mapping, visual management, Kaizen, etc. As a result, they may not realize that many of the processes that they perform everyday and the frustration that they feel at work are due to unnecessary waste. Additionally some workers are modest and reluctant to share ideas. It is management’s role to educate their staff on Lean tools and techniques that can be applied to the continuous improvement process and to help their employees overcome any personal or psychological barrier that prevents them from trying out new ideas.
Lean Tip #2755 – Continuous Improvement Requires the Right Environment
Applying continuous improvement requires participation from everyone in the organization. Upper management needs to invest time and money in employee training and empowerment. Managers need to foster an environment of trust, collaboration, open communication, and a willingness to experiment. And finally, workers need to be engaged in their work and be challenged to come up with small gradual improvements each and every day. By applying these principles, your company will be able to start and sustain your continuous improvement efforts. This will lead to a more economically competitive organization, more efficient work processes, and more satisfied employees.
Lean Tip #2756 – Review Your Week Every Friday.
Some people go to bed at night with a whirlwind of thoughts rushing through their mind. They hardly have any time to process what they have just done simply because they are so stressed out about what’s directly ahead.
Elaborating on his productivity quote, Farquhar says he sets aside a block of time each week to sit down and go over the previous week so he can answer three crucial questions:
1. Did I achieve what I wanted to achieve?
2. Did I personally need to be there for everything I attended?
3. Could I have achieved the same in a shorter timeframe?
This is a powerful tactic for determining whether you are really managing and spending your time wisely.
Lean Tip #2757 – Track Changes, Challenges and Breakthroughs
Self-reflection can aid in tracking changes, challenges that you face and breakthroughs in your life. Daily self-reflection lets you look back on where you have come from and helps you map out where you want to go in the future.
Even more, writing down a few thoughts each day will give you perspective. You may see that weeks, months, or years later, the things that you were so worried about didn’t have a long-term impact on your life.
Lean Tip #2758 – Understand Top Company Objectives
For effective priorities management, it's essential to practice upward alignment before attempting downward alignment. You could be managing the most unified, productive team on the planet, but if the goals they're achieving aren't furthering the objectives most valued by stakeholders, what will that get you?
If you aren't clear about overall business goals, not to mention your boss's objectives for you and your team, it could be a failing on the part of upper management. But sitting back and waiting for clarity to float down from on high will hurt you more than it hurts them.
So speak up. Be bold. Proactively manage your boss until you have the tools and information you need to succeed.
Lean Tip #2759 – Encourage Team to Make Time for Important But Not Urgent Work
Steven Covey's seven famous habits have now been in circulation for 27 years—an entire lifetime for many of today's enterprise workers. But it never hurts to be reminded of tried-and-true principles.
Covey suggested dividing work into four quadrants:
Important and Urgent
Important and Not Urgent
Not Important and Urgent
Not Important and Not Urgent
It's easy to find yourself spending too much time hanging out in quadrant three (Not Important and Urgent), and without a scorecard system to help you define universal standards of "importance," many of your team members will be.
After all, "urgent" is one quality that's easy to identify, while other qualities can be more subjective. Make sure your priorities management system is designed to keep your team in quadrants one and two most of the time, with extremely rare forays into quadrant four.
Lean Tip #2760 – Be Flexible Enough to Change Your Mind and Drop Priorities
As you prioritize, it’s important to remember to be flexible. No one knows what the future holds. And ultimately, prioritizing and planning is really just guessing.
Sometimes you might prioritize a task only to have expectations or deliverables change on you. At this point it’s hard not to be disappointed. But you can’t let that skew your judgment.
Humans are especially susceptible to the “sunk cost fallacy”—a psychological effect where we feel compelled to continue doing something just because we’ve already put time and effort into it.
But the reality is that no matter what you spend your time doing, you can never get that time back. And any time spent continuing to work towards the wrong priority is just wasted time.
Sometimes our effort is better used switching boats than trying to fix a leak.

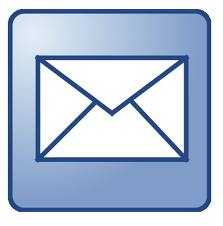



