What Is Lean Thinking in Manufacturing? A Practical Guide to Principles, Tools, and Benefits
Lean thinking is a philosophy that empowers organizations to create more value with fewer resources. It focuses on optimizing processes, eliminating waste, and continuously improving systems—all while keeping the customer at the center. Though there’s no single definition of Lean thinking, its foundations, principles, and practices offer a proven framework for enhancing efficiency and effectiveness in manufacturing environments.
In this guide, we’ll explore the core foundations of Lean thinking, the five lean manufacturing principles, and the rules-in-use developed by Toyota. You’ll also discover the benefits of Lean thinking, real-world examples of Lean in manufacturing, and how Lean compares with traditional methods.
3 Core Foundations of Lean Thinking in Operations
1) Purpose
In Lean production methods, the goal is simple: deliver maximum value to the customer. That value must be clearly defined and measurable so every team member understands what they’re working toward.
Whether you're streamlining a production line or optimizing logistics, a shared sense of purpose aligns efforts and enhances outcomes—making it a cornerstone of Lean management best practices.
2) Process
One of the key Lean thinking tools and techniques is relentless focus on improving processes. By identifying inefficiencies, eliminating waste, and enhancing flow, Lean organizations maximize value delivery.
Teams are encouraged to continuously evaluate and refine their processes. This commitment to quality and efficiency is what distinguishes Lean vs traditional manufacturing approaches.
3) People
A true Lean culture isn’t top-down—it’s collaborative. Everyone is empowered to contribute ideas, solve problems, and make improvements.
Leaders are mentors, not micromanagers. They observe, ask questions, and create the right conditions for people to succeed, aligning with the principles of Lean thinking for continuous improvement.
The 5 Lean Manufacturing Principles
Implementing Lean manufacturing principles ensures consistent delivery of value while minimizing waste. These five pillars guide daily operations in successful Lean organizations:
1) Identify Value
The first step in any Lean journey is understanding what value means to the customer. In manufacturing, this could mean product functionality, timely delivery, or cost-effectiveness.
Whether your “customer” is external or another department, identifying value is the foundation for improvement.
2) Map the Value Stream
A key step in Lean thinking in operations is value stream mapping. This involves detailing every step in the production process—from raw materials to finished goods.
Mapping helps highlight bottlenecks and eliminate non-value-adding activities, creating a blueprint for smarter workflows.
3) Create Flow
Once waste is removed, the goal is to establish smooth, uninterrupted flow. Products and information should move seamlessly from one step to the next with minimal delay.
This is a vital distinction in Lean vs traditional manufacturing—traditional systems often rely on batching and waiting, while Lean emphasizes real-time flow.
4) Establish Pull
Instead of producing based on forecasts, Lean systems use a "pull" approach—products are created based on actual demand. This Lean production method reduces overproduction, storage costs, and inefficiencies.
Pull systems are integral to just-in-time manufacturing, ensuring resources are used precisely when and where they’re needed.
5) Seek Perfection
Lean is not a one-time project; it's a continuous journey. Even the most efficient systems can be improved.
This principle reinforces the need for Lean thinking for continuous improvement by encouraging frequent evaluation, feedback loops, and iterative upgrades.
Four Lean Rules-in-Use from Toyota
To bring structure and discipline to Lean systems, Toyota established four practical rules—also known as Lean management best practices—that guide daily operations and problem-solving:
Rule 1: Specify All Work
Every task should be clearly defined in terms of content, sequence, timing, and expected outcome. This level of clarity allows for quick detection and resolution of any deviations.
Rule 2: Direct Customer-Supplier Connections
Every interaction between internal teams must be unambiguous. Communication paths should be simple, clear, and direct, with a binary yes/no format to request and receive work.
Rule 3: Simplify Pathways
Every product or service must follow a streamlined path to its destination. Services should not be randomly assigned but delivered to a specific person or station—enhancing accountability and speed.
Rule 4: Improve at the Source
Continuous improvement happens at the ground level. Frontline workers are empowered to refine their own processes, guided by supervisors and grounded in scientific thinking.
These rules help form a Lean production system where employees are not just executing tasks but actively improving them—boosting engagement and operational excellence.
Benefits of Lean Thinking in Manufacturing
Implementing Lean thinking in manufacturing offers measurable and strategic advantages:
- Increased efficiency: Eliminate bottlenecks and reduce downtime.
- Lower operational costs: Cut excess inventory and minimize waste.
- Higher customer satisfaction: Deliver what the customer wants—faster and more reliably.
- Greater employee engagement: Empowered workers lead to more innovative solutions.
- Scalability: Lean systems can grow and adapt with your business.
These are just a few benefits of Lean thinking that help businesses remain competitive in a fast-changing market.
Real-World Examples of Lean in Manufacturing
- Toyota Production System (TPS): The gold standard of Lean manufacturing, focusing on just-in-time production and continuous improvement.
- Nike: Used Lean to improve product flow, reduce lead time, and minimize environmental impact.
- Intel: Implemented Lean to streamline chip production, resulting in billions in savings and faster delivery.
These examples of Lean in manufacturing show the versatility and power of Lean across industries.
By understanding the Lean manufacturing principles, applying key Lean thinking tools and techniques, and adopting Lean management best practices, any organization can unlock its full potential. Lean is not just a method—it’s a mindset of continuous learning, adapting, and improving.
Whether you're just beginning your Lean journey or optimizing existing systems, embracing Lean thinking sets the stage for sustainable success in today's dynamic manufacturing landscape.
Need help applying Lean to your organization? Start with small wins. Map your value stream today and discover where you can deliver more value—with less waste.

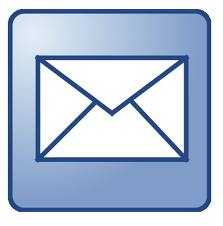





No comments:
Post a Comment