Successful
projects don’t just happen; they require hard work and collaboration from both
project managers and team members to ensure all tasks are completed and goals
are met, on time and on budget. However, many projects ultimately fail or are
abandoned because the team does not work together to achieve shared goals. Much
like how two people in a canoe won’t get anywhere if they’re rowing in opposite
directions, projects will be doomed to fail if all members are not working
towards the same end product.
To avoid this
unfortunate fate, project managers can find help with visual management and the
Obeya room. Visual Management is a Lean best practice used to inform and
involve anyone in the process (even those who are unfamiliar with the details),
and quickly allow them to see what is going on so that everyone ultimately
understands what is under control and what is not. A key element of Visual
Management is Obeya.
Toyota first
created Obeya rooms during production of the Prius in the 1990s. Since then,
organizations across many industries have put the concept into action. Obeya,
which means “large room” in Japanese, involves bringing together departmental
leaders to focus on big picture issues involved with a single project or
initiative.
Creating an
Obeya room is akin to creating a “war room,” a command center that draws
together leaders from across departments in an organization. While most often
associated with product development, Obeya also is useful as the command center
for managing a new business strategy, software development, project management
and workflow management. Obeya helps you to generate ideas, collaborate with
management and stakeholders, and gain a full overview of the projects and any
problems that need to be resolved.
An Obeya is not
a process island. Simply putting all of your engineers in a single, big room
does not an Obeya make. By the same token, a glass-walled room studded with
monitors displaying and rotating real-time data every 30 seconds also doesn't
qualify as an Obeya if it isn't used routinely to collaborate and manage the
business. While the room may be visually eye-catching, that may be all it is.
The idea behind
an Obeya is to break down the barriers that prevent employees from
collaborating and sharing information to make efficient decisions. Obeyas are
most effective when established and outfitted to solve singular problems or
work on specific projects.
Obeya rooms are
a process management tool that fuels creativity and collaboration between
decision-makers on all levels while developing problem-solving skills. An Obeya
promotes quicker, more nimble problem-solving by speeding up the
Plan-Do-Check-Act (PDCA) process.
Here’s a
breakdown of the PDCA cycle:
·
Plan: Define a problem and develop potential
solutions.
·
Do: Implement a proposed solution.
·
Check: Evaluate the results to see whether a
solution is working.
·
Act: Take one of two actions: return to the
planning step if the results aren’t satisfactory, or standardize the solution
if the results are sufficient.
Rather than
communicating across departments over the course of days or weeks, an Obeya
brings together key decision-makers to implement the PDCA cycle and develop
solutions quickly.
One of the most
essential components of a successful Obeya room is choosing what will be
visually represented in the room. Obeya rooms rely on visual management to spur
collaboration and it is important that only relevant and important information
is posted in order to keep the focus. For instance, posting customer complaints
will keep managers focused on meeting customer requirements and their
satisfaction. Other information that can be used in an Obeya are A3 reports,
KPI’s, and the results of previous projects. The documents posted in an Obeya
room should be clear and easy to understand, set up in a logical manner. It
should flow from one side to the other and tell a complete story.
Visibility of
information, transparency that applies to all relevant information, and visual
organization are important quality attributes. When you walk into a
well-equipped Obeya with your team, you would like to have easy access to
everything you need. Information should be clear so that there are no
misunderstandings. Then you are adequately enabled to identify improvements, make
decisions and take action.
But this is
just the foundational layer. First and foremost, it’s about the people. Nothing
happens with all that neatly collected information if there are no people
around willing to commit to each other and use the given platform to take
action in pursuit of process improvement.
The Obeya
connects information to people and therefore people to each other. By applying
a repeatable rhythm and fixed structure, people in the Obeya meet other experts
in their own field. All that expertise is needed to realize the strategic
intention of the organization. Team members evaluate the status of their work
and assess whether they are on schedule. Barriers can be discussed. Managers
assess where resources can be deployed and see, at a glance, what that could
mean for other initiatives.
Accountability
is further supported through frequent “daily” reviews, which highlight
responsibilities involved in executing project tasks and apply more pressure on
the implementation of corrective actions. For those looking to analyze and
improve their project processes more, this also can be great place to begin
your daily Gemba walks.
Companies using
an Obeya may enjoy a number of benefits. Those include:
·
Efficiency:
A project’s leadership team can save time by bringing helpful visuals,
necessary information, and vital resources together in one place
·
Focus:
Having key team members in the same room for collaboration and discussion means
that project leaders can focus on the right issues
·
Collaboration:
An Obeya fosters an environment in which employees can work together across
disciplines and in real-time, rather than via e-mail or in rushed meetings
For project
managers struggling to establish teamwork, visibility and accountability on
their projects, Obeya may be the solution. With the ultimate goal of breaking
down walls between team members and getting everyone working on the same page
together, Obeya rooms provide big gains in both collaboration and problem
solving, two features that are essential in project management.

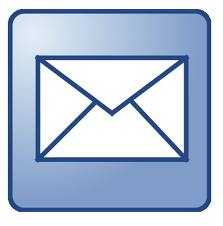




