
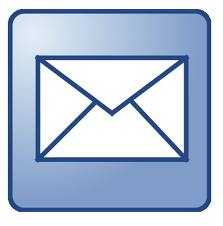





Almost
everyone has heard the saying, “April Showers bring May Flowers”. The saying
can be traced back to England from the 1500s poet Thomas Tusser. Back then, he
wrote “Sweet April showers do spring May Flowers”.
"April showers bring May flowers" is a reminder that even the most unpleasant of things, in this case the heavy rains of April, can bring about very enjoyable things indeed -- even an abundance of flowers in May.
Many of
life's greatest things come only to those who wait, and by patiently and
happily enduring the clouds and damp of April, you can find yourself more
easily able to take in the sights and smells of May. After all, it's easier to
love something if you begin with an optimistic outlook.
Have you had a season of setbacks, disappointments or hindrances? Do not be dismayed. Remember these things: there has never been a wind that did not change directions, clouds do not hang forever and April showers bring May flowers.
Those “April showers” are another way of saying today begins growing tomorrow. The habits I’m building right now, even if I’m not aware I’m building them, will be the color of my life in the future. Check your routine. Check your habits. Are you creating the “May flowers” you want?
Value is
calculated as a ratio of function to cost. A business can add value to a
product by either cutting down on cost or improving the function. Most
companies use value engineering as a cost-cutting strategy, where the basic
function of a product is preserved – not sacrificed – in the process of
pursuing value improvement.
Value
engineering can be broken down into the following phases:
1. Information
The information
phase involves gathering project information and refining the goals of the
project. They obtain project data, present the original design or product
concepts, and understand the project scope. Schedule, costs, budget, risk, and
other non-monetary issues are studied until the team is comfortable with the
concept of the project, what it is to produce, and who its end users are. Data
is collected and analyzed, and the information obtained is used to finalize the
priorities of the project and areas of improvement.
2. Function
Analysis
The function
analysis phase involves determining the functions of the project and
identifying them with a verb/noun combination for every element under
evaluation.
Functions come in four forms:
There can also
be all-the-time functions, one-time functions, unwanted functions, and lower
order functions.
Each of the
identified functions is analyzed to determine if there are improvements to be
made and if a new function is required. An example of a function can be
“disinfect water.”
The function
should be as non-specific as possible, to leave room for multiple options that
perform the function presented by the project. A cost is assigned to each
identified function.
3. Creative
The creative
phase follows the function analysis phase, and it involves exploring the
various ways to perform the function(s) identified in the function analysis
phase. This allows team members to brainstorm alternatives to existing systems
or methods that are in use.
Brainstorming
forces people to be creative and allows team members to speculate on all
possible solutions to the problems presented, or alternatives to the function.
The team is required to develop a list of potential solutions to the function
formulated by the verb/noun combination.
4. Evaluation
In the
evaluation phase, the merits and demerits of each of the suggested solutions
and alternatives from the creative phase are listed. The team should describe
each advantage and disadvantage in general terms.
When the
disadvantages exceed the advantages, the alternative is dropped in favor of
other solid alternatives. The team performs a weighted matrix analysis to group
and rank the alternatives, and the best alternatives are selected for
consideration in the next phase.
5. Development
Once the value
improvement options have been whittled down to the ones that make sense, the
value engineering team conduct an in-depth analysis of each best alternative to
determine how it can be implemented and the cost involved. The examination of
each alternative may involve creating sketches, cost estimates, and other
technical analysis. They must be clearly written and explained so that the
project owner and stakeholders can understand how it benefits the project and
act on it. Any potential negative factors are identified. Potential costs and
cost savings are itemized. Team members formulate an implementation plan for
the project, which describes the process to be followed in implementing the
final recommendations.
6. Presentation
The
presentation phase is where the team meets with the management and other
stakeholders to present their final report. The team is required to present
their findings to the decision-makers using reports, flow charts, and other
presentation materials to convince them that the final ideas from the
development phase should be implemented.
The ideas
should be described in detail, including associated costs, benefits, and
potential challenges. The final report acts as a record of the team’s
accomplishments during the study and a summary of the team’s deliberations and
findings. It can also act as a reference tool for the company in future
projects.
Implementation
of the project begins after the management’s approval of the team
recommendations. If there are changes requested by the management or other
decision-makers, these changes should be incorporated into the implementation
plan before the implementation begins.
When implementing
the project, the team should ensure that the primary goal of increasing value
is achieved. The actual cost savings of the project should be determined based
on the implementation of the recommendations.
‘April Fool was a great leader. She took care of her people, she was a great listener and she was empathetic. She was excellent at developing her team and helping them get promoted. Her character was impeccable and she was also great at getting results.
She was a great
leader on every day of the year except the first day of April. On April 1st,
she turned wicked and played tricks on her team. She thought they were funny,
but her team was annoyed and often fearful of her shenanigans. No one was safe
on April 1st when April Fool was around.
The
tomfooleries turned tragic when April died trying pull of a dangerous,
over-the-top prank. Her team wanted to honor her, so they started the tradition
of April Fool’s Day and it eventually expanded nationally. Very few people know
the true origin of the day.
This teaches us
a great lesson about using humor in the workplace. Leaders can use emotional
intelligence and humor to reduce anxiety as well as improve performance and
motivation. They can also help develop or reinforce a positive culture. Leaders
shouldn’t be afraid to introduce appropriate jokes and wit into the workplace.
Of course, the
story of April Fool is completely fake — but feel free to spread the hoax as
you see fit. Just for today.
A selection of highlighted blog posts from Lean bloggers from the month of March 2022. You can also view the previous monthly Lean Roundups here.
Do Your Job – Bruce Hamilton shares a story regarding CNC set-up reduction involving the need for a repeatable lathe process.
Strategy and the Worlds of Thought & Experience – Pascal Dennis says the movement between thought & experience is central to strategy and problem solving in general.
5 Ways to Be More Grateful and Why Lean Thinkers Should Care – Ron Pereira talks about how to deliberately practice gratitude.
Top 8 Reasons Teams Abandon Their Visuals – Jon Miller explains failure to maintain visual process standards is about “people” and shares the top eight reasons teams abandon their visuals.
Developing Leadership Through Tours – John Knotts discusses how you can use field trips to develop leaders in your organization.
If You’re Going to Visit the Gemba, Your Mindsets and Behaviors Matter… A Lot – Mark Graban says the behaviors of a leader in the gemba matter greatly and explains how to make them impactful.
A Lesson for Enabling Leaders and Systems – Josh Howell says an executive's gemba visit reveals the value of engaging value-creating frontline workers in improving their work processes and talks about how you can create systems and adopt behaviors that help them do so.
How the Toyota Way and Toyota Kata Fit Together – Jeffrey Liker the author of The Toyota Way explains where Toyota Kata fits with Toyota’s broader management principles — and how each enhances the other to help you build more effective organizations.
Ask
Art: How Does Lean Apply to Every Company? – Art Byrne shares a
back-to-basics explanation of why — and how — lean thinking and practices can
improve the performance of any company or organization.