I am a proud participant of the Western Massachusetts Lean Network. This is a network of Lean thinkers at various stages of their journey whose goal is to share best practices within the network as a way for all of us to continue learning. The Greater Boston Manufacturing Partnership (GBMP) is the host of our network. We recently started a forum for sharing online where we can post a question of the week.
I suggested the following question a couple weeks ago:
What are your thoughts on Lean in the office compared to Lean in a production setting?
I suggested the following question a couple weeks ago:
Does it seem more difficult to do administrative kaizen then production/operations kaizen? If so, why?Bruce Hamilton, President of GBMP and Vice Chair of Shingo Prize (aka Mr. Toast), gave an insightful response.
In responding to this question, the following comment from Shigeo Shingo comes to mind: "The real problem is thinking there is no problem." Having spent half of my career in administrative functions (marketing, IT, materials management), I'm well aware that there are loads of problems in the office environment. Information wells, disconnects, and mazes are normal as are correction loops. Office layouts create huge excess motion and encourage batching of everything from sales leads to factory and purchase orders to inspections to invoices – and finally collections. Every piece of information is batched with all the problems that attend that practice. (Of course there are occasional exceptions to this stereotype, so before continuing, I apologize to them.)My experience with Lean in the office mirrors that to which Bruce summarized. Lean is a building, thinking process which requires both learning and thinking by building on experiments. Bruce provides some logically first steps for any kind of improvement activity.
The barrier to engaging administrative departments is initially higher than in production for are several reasons:
• Top management is predisposed to round up the usual suspects when problems occur, and those suspects are in production. Management rationalizes that problems occur there because production employees are less well formally educated or because they are paid less and are therefore less likely to care about their work – or maybe they're tired from working a second job and therefore more prone to mistakes. None of this is true, of course, but production often faces this bias and then takes it on the chin when problems occur.
• Office employees take their lead from management and tend to have the same misconceptions about production. At the same time they have an unchallenged complacency for their own situations. While production has a long history of absorbing blame, office employees have remained mostly above the fray when problems occurred.
• Knowledge work" as it's called is not so visible and is mostly unscrutinized. Although waste in knowledge work is huge, office employees fly below the L,M&O radar.
• Office employees (including department managers) have more position power than factory employees and are therefore better equipped to fight change. Many a change agent has been derailed by choosing to battle a savvy office manager.
• Managers of administrative functions are often paid commensurate with the number of reports, so a system that may recommend few reports will not be motivating.
The challenge to overcoming these initial barriers is to:
1. First identify early victories that make the job "easier, better, faster and cheaper" (the theme of our October 19-20 Northeast Shingo Conference). Don't pick a project that involves work or them with benefit only to production (e.g. "Scheduling smaller batches" or "More timely and accurate forecasts.") Pick projects lessens their loads (e.g., "easier pricing system for order entry" or "better customer information for collections" or "printers in the right locations.")
2. Choose "small" projects that can be completed quickly and make sure resources (often IT) are available to complete the efforts.
3. Third, publicize victories to the stakeholders keeping in mind all of the objections and predispositions (and surrounding politics) implied in the points above. Share the success and give credit to managers and employees. Provide explicit descriptions of before and after conditions with hard numbers.
The bottom line is that administrative departments will buy-in once managers and employees understand the benefits and are persuaded that these far outweigh any potential threats. Your objective is to respect and answer their objections while they are learning.
What are your thoughts on Lean in the office compared to Lean in a production setting?

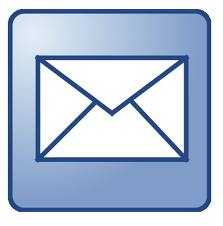





I think that it is the same problem that you face in services. A system thinking approach like that proposed by John Seddon is very interesting and I think better.
ReplyDeleteWe began lean approach in the office and it become an IT automation project. But I think that it has to be different from this.
Tim,
ReplyDeleteI’d say from my experience it does seem more difficult to complete office kaizen than production, the why?
1) Line Mentality – everyone in production can “see” the production line. They can walk it, touch it, they may not like the other parts of it, they may see others as the ‘problem’, but they at least appreciate that they are part of a chain. Often I’ve seen office based processes go from Marketing (one cost centre) to an external company, to deliver the marketing campaign, back office function (linked to finance cost centre) to process the initial enquiries, to a call centre (another cost centre) making bookings for salespeople (another cost centre) – the chain just isn’t visible to anyone.
2) Waste is hidden – see a machine on changeover or broken down, part-built orders waiting for supplies,sending parts back for re-work and it’s obvious there is a problem. Set a PC to crunch some numbers for 2 hours and no-one except the operator sees this, re-work paperwork and it's hidden. If you have a meeting once a month and information has to sit for 3 weeks and six days till some looks at it again, those days are not viewed as waste.
3) Processes are unwritten and unknown – not just manual paper processing ones but the “electronic information” processing rules. I’ve lost count of the number of businesses who when asked to explain the journey that electronic data goes on, can’t articulate it, if they think they can, we later discover they had it wrong.
4) Processing Cycle Time v Processing Time – as in most businesses, whether office or production based the functional design of organisations means that everyone is focussed on the latter. So we go for faster and faster PC’s, data capture and processing systems not realising that the data we’ve loaded really fast will still sit there till the 2am upload to the main server, or the paperwork we did at 1pm will sit till the 4pm internal mail man comes to pick it up and he’ll deliver it to the recipient at 11am next day.
5) Targets – in some, not all, production areas there is a target, weekly, daily for outputs so we know whether they are ahead, behind, need to run overtime etc. In many offices there is often no target, no watching for what is urgent, what is falling behind, what might require additional resources. Daily management, the huddle is not something, historically done in offices, hang your cost on the back of your chair, switch on PC, go to work!
We have come across the issues around ‘knowledge’ jobs which we work through by reviewing outputs and beginning to classify them. It often becomes obvious that they are using a set of processes.
Hope this insight from the other side of the pond helps.
Great blog by the way, some good insights on the other pages.
regards,
Mark
www.theleanmanager.wordpress.com
Luciano, Lean is a system approach. Perhaps we refer to these as processes. Still I think it is hard to separate the individual from the process for many. This creates a difficulty for some to be able to distinguish value vs non-value added activity. This is where you need to step into the customers shoes.
ReplyDeleteI think the challenge in office lean is the customer is not always visible so it is not easy for all to understand what is really value added.
ReplyDeleteI think offices also have a difficult time coming to grips that the majority of what they do is waste (albeit probably neccessary non-value added). Offices are prone to busy work and the need for cascading approvals before you can move on.
I read an interesting statement the other day that creative work can not be error proofed like manufacturing. In relation to Knowledge Work in an office, I think this statement proably seems true because good quality is not often defined. If you define good quality, you can then work towards error proofing. You may not eliminate all errors but the mindset that you can attempt to error proof will get better results than thinking "why try" because you believe creative work can't be.
Great post Tim!
Hi Tim,
ReplyDeleteGreat post! I think you, Bruce Hamilton and your community have gotten it right. One thing that I may highlight is the notion of transparency.
There are no "secrets" in lean. We need to easily see, identify and respond to abnormal conditions whether it be process performance or process adherence. This principle can be very intimidating to those within the office. They are not used to this type of transparency and, I dare say, accountability.
Great post. I have been wondering for a while if and how lean could be applied in the office. We have implemented TOC in our IT project processes and have faced similar issues. Around our projects we still have our "normal" office work which is neither TOC nor lean. One question remains for me, when is it a good idea to implement lean in the office? To be honest the stories I read here lead me to doubt if lean is a good solution for all offices, in some cases I get the idea you are digging a hole with a spoon (it can be done but is just not very practical/productive). Seems like there must be some basic criteria that the office work should meet before considering lean as a solution.
ReplyDeleteJustTOCit, For me lean is a thinking methodology based on prodiving customer value in the most efficient means. So Lean works in any environment as has been show in the last several decades. There is no wrong time to implement Lean Thinking nor any right time. I am not sure what types of stories you are referring to but they sound L.A.M.E. (Lean As Misguidedly Executed). True Lean in my experience is very possitive in any workplace.
ReplyDeleteIn Lean we analyze the process that it takes to make something or deliver a service. The goal is to make the process as effecient as possible in terms of the customer's values. This inlcudes internal and external customers. All processes can be improved which is a basic belief of Lean Thinkers. Therefore there is no minimum criteria. I would add that everyone process, every organization is different so naturally are their problems. Hence, different solutions need to be applied to different problems. This is where the thinking comes in. The tools in the Lean Toolbox help with this.
I coordinated a "Community A3" a few months ago to address the problem of meeting waste. My thinking was similar to your upcoming Shingo Conference: identify early victories that make the job "easier, better, faster and cheaper," and could be done without adding resources at all.
ReplyDeleteAs they worked through their A3s, participants learned the staggering cost of ineffective meetings, and came up with ways of improving their situations. A group in one company decided to move to a "pull system" for meetings -- only having them when there was a need.
To your point(s), though, it's difficult to root out waste until you're able to see it and quantify it. But even selecting a small, manageable target like meetings was useful in inspiring people to go further and attack larger issues.