Who are you and what do you do?
I write, teach, and consult on Lean Manufacturing, and have been at it since 1987. Within Manufacturing, I have worked on Lean implementation in industries ranging from frozen foods to aircraft, on four continents. I have occasionally ventured outside of Manufacturing and to topics other than Lean, but have always come back. Overall, since 1981, I have been working to understand the human and technical dynamics of manufacturing, and to contribute to their improvement. Why did I choose this field? It was not the direction I had started in.
I was born and raised in France, and studied Engineering there in the 1970s. The French-Lebanese writer Amin Maalouf wrote that people should view themselves as having origins rather than roots. Origins are where you came from. They don’t restrict you. Roots hold you in one place like a tree. I have lived 31 years in the US, 23 in France, 4 in Japan and 1 in Germany. And I have visited other countries on consulting assignments. I am from France, but have immersed myself in other cultures from an early age. This is why and how I have learned English, German and Japanese well enough to function professionally in these languages.
How and when did you learn Lean?
In 1980, I was a researcher in probability theory, working out results that were later published in 81, 83, 84 and 86. This theoretical work was intended for earthquake prediction, which had led me to Japan in 1977. By 1980, I had understood that this pursuit was futile and the task impossible with the available technology. As of 2012, it still is.
As a French draftee with knowledge of Japan, in late 1979, I was assigned to the Scientific Service of the embassy in Tokyo, where part of my job was organizing and leading factory tours for visiting industrialists. Their reactions made me realize that there was something special to these factories, and it piqued my curiosity.
One of my colleagues, Francis Lecroisey, told me that Toyota had developed a remarkable production system and that I would find at least two books about it in any neighborhood bookstore in Tokyo. It was true, as I checked down the street from my apartment. To this day, when I visit Japan, I still hit the larger bookstores for the latest about Manufacturing, and find hundreds of titles on topics ranging from cell design to quality and company-specific approaches. This literature, unique to Japan, is targeted at practitioners and full of concrete, actionable ideas, clearly and graphically explained.
How and why did you start blogging or writing about Lean?
I have always wanted to be a writer when I grow up, and I still do. Blogging is to book writing as one-piece flow is to batch production. On a blog, you publish small pieces and receive immediate feedback in numbers of page views and comments. With a book, it takes two years of hard work before you find out whether your intended audience is interested in what you have to say on a subject. I learned both Lean and the means of implementing it by working with Japanese consultant Kei Abe for eight years. In the beginnning, I made myself useful to him by generating slides and writing reports to clients. Later, these slides became the basis for my initial course materials, and the reports, duly sanitized, for my books and articles.
I didn't start blogging until a year ago. Until then, I participated in discussion groups, particularly NWLEAN on Yahoo, where I was the most prolific contributor. For years, it was the most active forum on Lean, but it is now dwarfed by LinkedIn groups. NWLEAN topped out at about 6,000 members; the Lean Six Sigma group on LinkedIn, as of this morning, has 144,717. But LinkedIn has many groups on Lean, with overlapping memberships.
Blogging has the following advantages over participation in discussion groups:
- You have full editorial control.
- You can format and illustrate the content with photographs and even videos as you see fit.
- Everything you write is concentrated in one place.
And you can still participate in most LinkedIn groups by sharing your blog posts.
What does Lean mean to you?
I define Lean Manufacturing as the pursuit of concurrent improvement in all dimensions of manufacturing performance by eliminating waste through projects involving both the production shop floor and the support activities.
To me, it is essential to Lean that the changes you make do no harm. For example, you don't improve quality by sacrificing productivity or lead time. You focus on ways to improve all at the same time, which, by simple logic, leads you to focus on waste and takt-driven production. But you don't go around with a checklist of waste items to eliminate. Instead, you structure the transformation into projects like cells, chaku-chaku lines, SMED, milk runs, or Kanbans, each of which addresses many instances of waste at once.
I think this definition is applicable with small vocabulary changes to other types of businesses, but my concern is Manufacturing.
What is the biggest myth or misconception of Lean?
The engineering dimension of Lean is given short shrift, just about everywhere outside of Japan, and it is the main reason so many implementations fail. A complete approach covers all the four dimensions that my colleague Crispin Vincenti-Brown identified:
- The manufacturing and industrial engineering of production lines and work stations.
- Logistics and production control.
- Organization and people.
- Accountability.
In the US, you do see some milk runs and Kanbans, some production teams, and performance boards. Logistics, organization and accountability do get some attention, but engineering doesn't, except from the few Lean consultants with an engineering background, who think nothing else matters.
In reality, everything matters. If you want Lean implementation to succeed, you can't leave out any of the four dimensions, which doesn't mean you address them all at once. Engineering is the foundation, and usually where the low-hanging fruits are to be found.
What is your current Lean passion, project, or initiative?
I have a particular interest in manufacturing data mining. In my practice, wrangling information out of clients' legacy systems has always been one of my strengths, and I would like to share both the kind of results I found and the methods I used with the community.
However, even though my clients find this work useful, I have yet to find disciples. Last year, we offered a class on this subject through UC Berkeley extension, but no one signed up. The announcement was as follows:
Recommending a road-map to Lean for a plant requires understanding its business and its technology. Much -- but not all of this understanding -- can be gained by directly observing the shop floor and listening to managers, engineers, and operators. Direct observation and human perceptions, however, must be supplemented by data mining. Among the sources the analyst must draw on for this purpose are the data generated by manufacturing operations: production is driven by orders converted to schedules, it is performed according to specs, its status is monitored and results are recorded both in terms of quantities and quality.
The size of manufacturing data sets permits analysis to be done with tools that are either already present on engineers’ laptops or can be downloaded at little or no cost. Focused data cleaning is the most challenging first step. Making clean data talk requires tools that are much simpler and easier to use than those described in the data mining literature. The effective presentation of the results requires focusing on graphics for communication, not decoration.On my blog also, posts on this subject generate little echo, so I am keeping this bag of tricks to myself for now. My posts on metrics, on the other hand, have the most page views and comments. Through the blog, my audience is telling me to pivot rather than persevere...

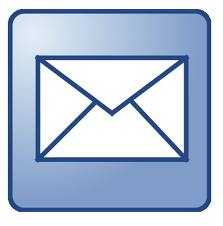





No comments:
Post a Comment