Click this link for A Lean Journey's Facebook Page Notes Feed.
Here is the next addition of tips from the Facebook page:
Lean
Tip #1186 - Give People Ownership
Let
employees make projects their own, to succeed or fail at. Employees need to be
encouraged to create solutions independently of the chain of command. This
leads to independent thinking.
Lean
Tip #1187 - Make Risk-Taking and Failure Acceptable
Many
organizations avoid risk like the plague, and have low tolerance for failure.
To give rise to entrepreneurs, leaders and managers need to develop a culture
of learning from failure that moves on to the next, more informed attempt…otherwise
known as experimentation. Actively encouraging learning is key.
Lean
Tip #1188 - Give Employees the Time to Innovate Outside their Current Job Roles.
Employees of LinkedIn are given three months to pursue and promote new ideas.
It should also be noted that some determined employees will go above and beyond
the call of duty and develop ideas on their own time.
Lean
Tip #1189 - Have a Vision for Change
You
cannot expect your team to be innovative if they do not know the direction in
which they are headed. Innovation has to have a purpose. It is up to the leader
to set the course and give a bearing for the future. Great leaders spend time
illustrating the vision, the goals and the challenges. They explain to people
how their role is crucial in fulfilling the vision and meeting the challenges.
They inspire men and women to become passionate entrepreneurs finding
innovative routes to success.
Lean
Tip #1190 - Fight the Fear of Change
Innovative
leaders constantly evangelize the need for change. They replace the comfort of
complacency with the hunger of ambition. ‘We are doing well but we cannot rest
on our laurels – we need to do even better. ’They explain that while trying new
ventures is risky, standing still is riskier. They must paint a picture that
shows an appealing future that is worth taking risks to achieve. The prospect
involves perils and opportunities. The only way we can get there is by
embracing change.
Lean
Tip #1191 - Use Positive Words to Create a Gracious, Polite Workplace in Which
Staff Feel Recognized and Rewarded.
Say
thank you. Show your appreciation for their hard work and contributions. And,
don't forget to say please often as well. You did a nice job on that
presentation, Jim. Those charts were easy to follow and gave me a great
overview of your progress on the project, Elizabeth. Social niceties and
compliments do belong at work. A more gracious, polite workplace is appreciated
by all.
Lean
Tip #1192 - One of the Best Forms of Recognition is to Provide Opportunities
for a Contributing Employee.
Opportunities
can take many forms. But, all of them are outside of the normal day-to-day
requirements of their job plan. Employees appreciate chances for training and
cross-training. They want to participate on a special committee where their
talents are noticed. They’d like to lead a team that is pursuing an important
objective.
Lean
Tip #1193 - Never Underestimate the Value of Sharing Your Time and Building a Relationship
with Staff.
They
appreciate your genuine interest in their ideas and thoughts about their jobs.
They like bouncing ideas back and forth with you and look for your sincere
input on their projects and goals. The role of mentor and coach is powerful in
training your organization’s culture and expectations. It is also a significant
source of experiential knowledge, history, work approaches, and on-the-job
training.
Lean
Tip #1194 – Create a Recognition Culture.
It’s
easy: Just make recognition something you measure. One of my old bosses started
every management meeting by having every supervisor share two examples of
employees they recognized or praised that day. At first it seemed cheesy and
forced, but we quickly embraced it.
Plus
there was a nice bonus: Peer pressure and natural competitiveness caused a few
of us to help our employees accomplish things worthy of praise so we had great
stuff to report.
Lean
Tip #1195 - Hold Yourself Accountable.
As
a leader, it’s your responsibility to keep your employees motivated and
engaged. Put in the time to learn about each of your team members so that you
know what incentives and rewards are most attractive to them. When the time
comes, provide successful employees with recognition and rewards that are
specific to them.
Lean
Tip #1196 - Educate Your Workplace.
Like
any other business strategy, ongoing education of the workplace is critical in
establishing awareness, developing skills, and institutionalizing the needed
mindset and behaviors to bring about effective change. It is no different with
Continuous Improvement. Expect and overcome resistance to change with ongoing
training, reinforcement of expected behaviors, and recognition of those who are
learning and doing.
Lean
Tip #1197 - Establish an Enduring Culture.
For
continuous improvement to work, there must be a relentless focus on and
commitment to getting things right. Adaptability and an action oriented
leadership team are inherent components of a continuous improvement culture.
Resistance to change exists in all organizations to a degree and it must be
recognized for what it is, an impediment to improvement.
Lean
Tip #1198 - Establish Improvement as a Core Value.
Establish
the core values that comprise the continuous improvement culture such as a
focus on supporting the customer, teamwork throughout the extended enterprise,
receptivity to evolving continuous improvement concepts and tools. These core
values will create a sense of belonging and a common vision for all involved.
Lean
Tip #1199 - Communication Planning is Essential for Improvement.
Ensure
regular communications to foster collaborative interactions among leaders,
stakeholders, and practitioners at all levels. Take advantage of communications
techniques appropriate for the information being conveyed. Where needed,
schedule face to face meetings and where not needed, use the communication and
collaboration tools and capabilities of the enterprise to keep all members
updated and involved.
Lean
Tip #1200 - Use a Consistent Approach for Improvement.
A
consistent and structured approach for project identification and execution
will provide the organization with the ability to identify, select, and manage
continuous improvement projects. The continuous improvement project process
should also provide post-closing process steps to continually refine the
improvement project methodology and to act upon the lessons learn from the
project effort.

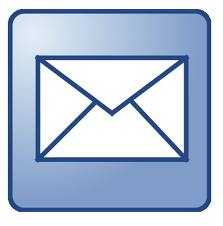





No comments:
Post a Comment