A Lean Enterprise is centered on the concept of flow. Flow is one of five key Lean Principles identified by Womack and Jones in their book Lean Thinking. They stressed that you need to make value flow. It was this creation of flow that would make it possible to eliminate waste. When material and information flow continuously, there is less waste in the system. This is true by definition. If there were a lot of waste, material and information would not be flowing.
The
first step is to focus on the analyzing the value stream. Find out why the
inventory is necessary and what purpose the work in progress is serving, then
reduce the amount of things that are waiting around. If frequent machine breakdowns are the
problem, then focus on the machine and reduce the stoppages. If the quality is
unstable, then repair the equipment and standardize the workers’ processes to
reduce variability. If people are holding inventory because they are afraid of
running out of parts, then talk with the leader of the area and decide how many
parts should be held. As the ability of
the area improves, the inventory can be reduced accordingly. Focus on the
foundation of the value stream. Keep reducing the amount of things waiting
around and get closer to flow.
Once
the amount of things that are waiting is reduced this will mean that you have
less time to solve problems that occur in everyday operations. Problems will appear faster, and also will
affect other areas faster. This is actually the desired result. Many things in
the company will now have to speed up to prevent production stoppages. Once you
get enough strength, you can continue to reduce the amount of inventory.
Creating
flow gets production and engineering involved. People have to come up with
improvement ideas. Kaizen involves every employee - from upper management to
operators. Everyone is encouraged to come up with small improvement suggestions
on a regular basis.
Once
you get to one-piece flow then you can make a Kanban for the line and start
with a downstream pull system. As the name suggests, creating flow is about making and
moving one item at a time (or the smallest batch size possible) through a
series of uninterrupted steps, with each step in the process making exactly
what is requested by the next step while never knowingly passing poor work
forward.
Flow
is often not actively pursued because people feel it is more realistic to
eliminate waste from work processes, introduce workplace organization through
5S or apply other lean tools. This is a mistake – it turns out that, when you
introduce flow into any process, problems (i.e., opportunities to deliver
customer value) become vividly apparent and demand immediate attention.
Introducing flow can be a bit scary, but it can also sharpen your focus on
improvements that will be immediately felt by your customers!
A
consistent flow of work is essential for faster and more reliable delivery,
bringing greater value to your customers, team, and organization.

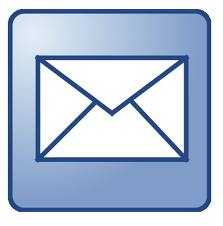





No comments:
Post a Comment