![]() |
Courtesy of Lean.org |
There is no room for compromise in Lean when it comes to quality. Jidoka incorporates quality checks into every step of the production process by providing machines and operators the ability to detect when an abnormal condition has occurred and immediately stop work. This enables operations to build in quality at each process and to separate men and machines for more efficient work.
The term Jidoka used in TPS (Toyota Production System) can be defined as "automation with a human touch." At Toyota this usually means that if an abnormal situation arises the machine stops and the worker will stop the production line. Autonomation prevents the production of defective products, eliminates overproduction and focuses attention on understanding the problem and ensuring that it never recurs.
It is a quality control process that applies the following four principles:
- Detect that something has gone wrong.
- Stop.
- Fix the immediate condition.
- Investigate the root cause and install a countermeasure.
Jidoka highlights the causes of problems because work stops immediately when a problem first occurs. This leads to improvements in the processes that build in quality by eliminating the root causes of defects. In this way, Jidoka is often used in conjunction with structured problem-solving tools.
The implementation of Jidoka relies on a mix of cultural concepts and Lean tools that are summarized below.
Developing a Jidoka mindset. Many people are trained to react to problems and to put in place quick fixes. The concept is to keep things running for as long as possible and work around problems as quickly as possible. A Jidoka mindset is different in that it says that, in the long run, efficiency will come from addressing the root cause of problems and that investing time in solving problems is a valuable investment.
Empowering staff to ‘stop the line’. Do your staff feel that they are empowered to say ‘stop’ when they see an unsafe act or a problem occurring? Many organizational cultures, through the words and actions of managers, disempower staff from stopping a process. Developing a culture where people feel that they are able to raise a real issue – and that far from being penalized they will actually be thanked for raising the issue – is very important in jidoka.
Installing andons. Andons are audible, or more commonly visual, signals that something has happened. The aim is that andons quickly alert managerial and technical staff to a problem having arisen so that they can get to the source of the problem and begin to investigate it.
Solving the root cause. Quick fixes are typically just that. Jidoka relies on the implementation of an immediate fix to stem the potential damage and on the longer-term fix that comes through root cause analysis.
Utilizing standard work. Having implemented the changes it is vital to document what has been done and to carry out any training required on the new process.
Selective automation. Selective automation is about investing in technology to detect – and more ideally prevent – errors arising wherever there is a business case to do so. This means wherever there is either a high probability that things will repeatedly go wrong, or where a problem arising has significant impact (such as the ability to cause harm), then it means investing in sensors and other systems to enable you to control the process and detect problems as early as possible.
As you can see, Jidoka combines the concepts of mistake proofing, TPM, standard work, structured problem solving and the creation of a Lean Culture – the clustering of concepts under one heading is a feature of many higher level Lean tools and concepts. Jidoka is about quality at source, or built in quality; no company can survive without excellent quality of product and service and Jidoka is the route through which this is achieved.

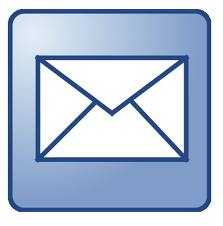





Hi Tim
ReplyDeletehere in europe almost every press article is titled Industry 4.0 :-) I strongly believe, that first of all most of SME owners still have other themes to cover and second, we already do quite a lot of automation in the industry but never you used this terminology the last 20 years. So, the idea of Industry 4.0 is based on a combination of Jidoka and automation. What do you think? Gerhard