Many business
leaders envision lean initiatives as massive endeavors that require long
training sessions, big meetings, and complete overhauls. Yet the reality is
that some of the most successful lean initiatives begin with a commitment to
creating a culture that’s focused on small, continuous improvements. It’s the
only way to achieve the long term company goal. Continuous improvement refers
to constant improvements of products, processes and services over time, with
the goal of improving product performance, customer service and workplace
productivity. You have to be aware that there is always room for improvement,
there is always a way to do it better.
In business,
continuous improvement especially refers to focusing on activities that add
value, and reducing everything else (the so called waste). Value added
activities are those things that customers are willing to pay for, while everything
else is a waste. And all waste should be eliminated (deleted, delegated),
simplified (automated, reduced) or integrated (merged) by the Kaizen mindset.
Kaizen is the
Japanese word for a “good change” (Kai = change, Zen = good). It means continuous
improvement of all company functions, at every hierarchical level, from CEO to
the least paid employees. It doesn’t matter if the change happens one time or
is constant, big or small, as long as it is a change for the better.
Kaizen is a
philosophy of continuous improvement in which every aspect of the business can
and must be improved. It is a process that engages the “human element,” while
eliminating all forms of non-value added activity and waste. Your workers’
talents and perspective are your company’s most important assets. Through
Kaizen, it’s possible to harness your team’s collective focus and
systematically improve all areas of your business – from individual steps in
the manufacturing process to behind-the-scenes administrative work.
When you
implement Kaizen you:
- Focus on standardizing your current work processes, and then developing incremental improvements on them over time
- Create a culture of problem solving employees who are constantly on the lookout for waste, inefficiencies, and opportunities for change
- Empower managers and employees at all levels of the organization to contribute their ideas on a regular bases
- Set a new standard where the expectation is that the company’s operations get a little better each day
Ensuring your Kaizen
is successful requires groundwork. It
begins by evaluating and understanding the current situation. Envisioning a
project with a start and end date is easy; it’s how most companies operate. Make
sure the process owner or sponsor is involved and in full agreement with the
process improvement activity. Also, make
sure the employees understand the goal of the improvement is to “work smarter,
not harder.” Solicit their input and
suggestions on how to make the process better. Getting everyone involved and in
agreement that the process can be improved will help make your Kaizen event a
success.
Follow these key
Kaizen principles for success:
- Continually improve.
- No idea is too small.
- Identify, report and solve individual problems.
- Focus change on common sense, low-cost and low-risk improvements, not major innovations.
- Collect, verify and analyze data to enact change.
- Problems in the process are a major source of quality defects.
- Decreasing variability in the process is vital to improving quality.
- Identify and decrease non-value-added steps.
- Every interaction is between a customer and a supplier.
- Empower the worker to enact change.
- All ideas are addressed and responded to in some way.
- Decrease waste.
- Address the workplace with good housekeeping discipline.
The result of
Kaizen should be a better workplace, a safer environment, elimination of hard
work, teaching people how to scientifically innovate and test new ideas,
reducing waste, increasing productivity, optimizing the supply chain and sales
channels, and so on.
You can always
do it better, make it better, and improve it, even if things are not broken. In
Kaizen, problems are seen as opportunities to improve.

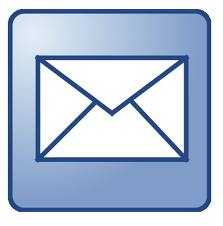





No comments:
Post a Comment