Click this link for A Lean Journey's Facebook Page Notes Feed.
Here is the next addition of tips from the Facebook page:
Lean Tip #2221 – Get Your Team to Show Appreciation
for Each Other
One easy and rewarding thing you can do to
create a positive working environment is to actively show appreciation for your
team, and encourage them to show appreciation for each other. This can be done
in an unstructured way, by just encouraging your employees to be thankful to
each other.
Lean Tip #2222 – Celebrate Team Wins
A team that celebrates together, stays
together. You will discover that most successes you have in your work are not
down to one person, but a whole team. Be sure to celebrate wins in the
workplace, no matter how big or small. This will not only help people to feel
appreciated but also make them understand that they are having an important
impact on the organization too! Get your team to decide on how they would like
to celebrate their next win. This will help them feel more invested in their
goal.
Lean Tip #2223 – Spend Time Together Not Working
Your employees are human, not resources or
man-hours. Take some time to do a non-work related activity together. This can
help to rejuvenate the team and also help them to see each other beyond their
job title. If your team feels relaxed and comfortable in each other’s presence,
this will create a positive and safe working environment.
Lean Tip #2224 – Set Boundaries and Expectations
Together
Create a positive and safe environment together
by conducting a workshop where your team can set boundaries and expectations
together. By creating these commitments together you will avoid team members
from feeling that something has been ‘imposed’ on them, and instead they will
feel more committed to the team's boundaries and expectations as this is
something they have created together.
Lean Tip #2225 – Trust Your Team
As a leader, it is essential that you trust
your team. Avoid micromanagement, or taking over tasks that others should be
responsible for as this will cause your team to harbor negative feelings.
Instead, nurture an environment of trust and give your team freedom (with
responsibility, of course) and this will spread positivity throughout your
employees.
Lean Tip #2226 – Encourage Your Employees to Chat
Face-to-Face
While sending a quick email or chat message to
a coworker might seem like a more efficient way of getting an answer,
oftentimes it can have the opposite effect, as the subsequent back-and-forth
can take longer than a quick face-to-face. Face-to-face interaction really
speeds up the process of solving a problem, answering a question, or getting
something important clarified.
Lean Tip #2227 – Hold a Daily, 10-Minute Company
Meeting
While meetings are generally considered a
necessity, they can carry on to the point where they eat away at the work day.
Each day gather as a company for a 10-minute meeting called the Daily Huddle. The
meeting serves as a firehose of information that keeps everyone in the loop,
including a roundup of key performance indicators, the celebration of
accomplishments, and the identification of opportunities to improve.
Not only is it a good way to keep all employees
up to speed on any new developments within the company, keeping meetings short
and sweet forces a streamlined meeting process, and reduces time wasted.
Lean Tip #2228 – Promote a Culture of Open Communication
Encourage your employees to communicate openly.
But, that goes beyond the idea of communicating face-to-face to solve problems;
do your employees feel comfortable voicing their concerns, or giving feedback
on how your company is run?
The best way to improve business efficiency is
to encourage feedback, ideas, and communication between departments. You can’t
be everywhere at once, nor will you see everything. Your employees may be able
to spot an area of your company that could be made more efficient, or a process
that could be streamlined. Make sure they feel comfortable voicing their
opinions, and offering feedback, especially when it comes to improving
efficiency.
Lean Tip #2229 – Communication is King
There's one simple thing that every business
can do that, if implemented, would change their business dramatically. That is
the communication process between management and employees. Nothing is more
effective than creating an efficient system whereby people can easily
communicate with anyone in one's company and someone actually responds. More
time and energy is wasted by people getting lost in a bureaucracy where
employee needs and questions are not met in a timely manner. Fix this and
productivity soars!
Lean Tip #2230 – Inspire Employees
Employees are the eyes and ears of your
business operations. If there are weak spots in your system, it’s likely
employees know about them. It’s also likely they want a better process for
completing tasks. But when your staff thinks you’re a “my way or the highway” leader,
they usually aren’t motivated to come up with solutions.
Involve your employees in improving business
operations. Ask your staff where improvements can be made. Take notes of the
flaws that are pointed out and solutions offered. Make sure your employees know
their opinions matter and you are open to suggestions. In addition to
accelerating your business process improvement, showing your employees that
they add value to your small business can take the stress off of your staffing
management plan by keeping employee turnover at a minimum.
Lean Tip #2231 - Don’t Resist Change.
While your gut reaction to change is often
refusal, such a response is not productive. Change is inevitable, and you must
learn to accept it. The quicker you do, the smoother your transition.
Lean Tip #2232 - Find the Positive in Change.
Even the most difficult changes can produce
positive results. Don’t waste time dwelling on what you don’t like. Focus
instead on the potential benefits and new opportunities the changes may bring,
and your spirits will remain lighter throughout the transition.
Lean Tip #2233 - Focus on One Change at a Time.
While we can learn to accept and manage change,
piling numerous changes up all at once can become too overwhelming, even for the
most flexible of us. If there are many changes going on in your work life, this
is probably not the best time to also start those home renovations. Managing
change in one area of your life is easier when you have other areas that remain
familiar and comforting.
Lean Tip #2234 - Encourage Flexibility
To transition through workplace change
successfully, workers need to be flexible. Encourage employees to embrace
change by engaging in new job responsibilities and facing challenges head on.
Be a role model to workers in your organization by getting out of your own
comfort zone.
Lean Tip #2235 - Involve Employees in the Change
Process.
Employees are not so much against change as
they are against being changed. Any time managers are going to implement
organizational change, there is always a lag between the time the change has
been discussed at the management level and the time the change is going to be
implemented. Managers like to play like an ostrich and believe that they are
the only ones who know about the changes that are going to take place.
Unfortunately, while their heads are stuck in the sand believing that no one
else knows, employees are effectively undermining the future changes with
negative informal communication…the company grapevine. The sooner you involve
employees in the process, the better off you will be implementing the change. A
formal communication channel is more effective at implementing change than a
negative informal one.

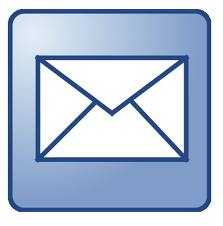




No comments:
Post a Comment