The goal of Meet-up is provide you an opportunity to meet some other influential voices in the Lean community. I have asked the following series of questions to which he has responded:
Who are you and what do you do?
My name is Matt Wrye. I am a internal lean consultant for a large consumer goods company. I am part of a group that is responsible for driving results for the company through lean thinking while transforming other areas of the business to lean thinking.
How and when did you learn Lean?
I started learning about lean in 1996 when I was doing an internship during college. My manager had me read "SMED" by Shigeo Shingo. My degree is in Industrial Engineering so there was a lot of lean concepts and tools I began to use. In 2001, I started working for an automotive supplier. The company's new President declared we were going to be lean. Three of us started reading and learning as much as we could and then went to the floor to try it. We made a ton of mistakes but had the opportunity to correct them. In 2007, when I switched jobs and was responsible for starting the lean initiative at a new company. At that time, I met Jamie Flinchbaugh. Jamie has been my coach for the last 5 years and during that time my understanding of the principles and thinking have developed to go along with the understanding of tools and concepts. It has been a long road.
How and why did you start blogging or writing about Lean?
I had two purposes when I started the blog. 1) Help get the message of lean out through the eyes of an implementer and 2) Improve my writing skills. I started by writing 3 or 4 guest blogs for Mark Graban at the Lean Blog. I couldn't stick to it though, so I took the plunge and started Beyond Lean to give more rigor to achieving the two purposes I outlined. I have found I really enjoy helping others learn. I hope I can provide them with information so they won't have to make the same mistakes I did.
What does Lean mean to you?
What a tough question. Lean is so big it is hard to capture what it really is or means, but here is my best shot about putting it into words. Lean is a way of thinking. It isn't about tools or concepts. It is about doing the right thing to add value for the customer in the least wasteful way while developing and respecting people.
What is the biggest myth or misconception of Lean?
Lean is not about eliminating waste. It is about adding value for the customer in order to grow revenue. In order to grow revenue and remain profitable though you want to eliminate waste so you can free up resources to use for new opportunities without having to add more resources/capital.
What is your current Lean passion, project, or initiative?
My passion is developing others' lean thinking. I really enjoy seeing others start to understand things through a lean lens.

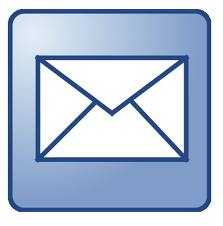




