Who are you and what do you do?
My name is Joe Wilson. I currently work for a pharmaceutical company and also have worked in the meat processing and automotive industry, mostly in a variety of Industrial Engineering and Continuous Improvement roles. I am also a contributor to the Beyond Lean blog.
How and when did you learn Lean?
I guess my formal training started when I worked for what was then a Dana plant where I got to take part in a formal kaizen event. The event itself wasn’t that memorable, but I was fascinated because the training material seemed to codify a lot of the way I already thought. After that, I went to work for a company that was all in on Eli Goldratt and Theory of Constraints, so I got to see a different angle of the CI picture. From there, I went to work with Matt Wrye (not because of him, but that’s where we met) and had the opportunity to really go deep with being a part of a Lean conversion. I also got to work with somebody who later went on to a supplier development position with Toyota who was invaluable in helping to informally coach me and close some of the theory gaps in my mind. I had some evolution in my role there that allowed me to spend time developing my formal problem solving skills, including working with some incredibly talented Shainin Red X problem solvers and a passionate Six Sigma Black Belt. There have been some formal classes and certifications and thousands of hours of self study.
How and why did you start blogging or writing about Lean?
Matt may remember it differently (and his version is probably right), but when he told me about starting up Beyond Lean, I told him to let me know if he wanted any help. He told me that if I ever wanted to contribute, he would let me guest post. That evolved at the beginning of this year to a more permanent role as an author. Unfortunately, because of some other time-sucking issues, my contributions have been a little more sporadic than I would like. For me, the writing is the easy part…it’s the editing part that kills me.
What does Lean mean to you?
Personally, Lean is that example that I can point to when I’m trying to make a point that other people can’t see. It is leverage in trying to change the way other people think about their work. It’s a community of people who allow me to validate or challenge my existing ideas about what’s possible. I don’t have a clue in the “chicken or the egg” argument of whether or not Lean makes me think this way or if I think this way and it aligns with Lean. I just know that Lean fits for me.
What is the biggest myth or misconception of Lean?
It seems lazy, but I’ll fall back on the whole “Lean is not a collection of tools” line. Let’s be honest, when most people talk about “lean”, what they are talking about is the understanding of what Toyota has done. In that sense the discussion revolves around trying to study somebody else’s solutions to their problems. To me, breaking down specific tools makes for some enjoyable philosophical and theoretical conversation, but it often seems like a distraction when you are trying to actually do something.
What is your current Lean passion, project, or initiative?
Professionally, I am focused on the concept and practice of how problems are defined. I don’t mean that in terms of an individual problem or for an A3. What I mean is, organizationally, how are we going to identify what is and isn’t a problem, what scale the problem is, and how we are going to dedicate resources to solve the problems. Toyota’s system became what it is because they made certain decisions along the way that shaped what they will and won’t do. I believe everything else (from a CI perspective) flows from that point.
Personally, I’m on a quest to see if there is such an animal as “Lean Six Sigma”. Although I’m “certified” in both Lean and Six Sigma, I have never been able to understand how the two could merge. So far, the closest mental model I’ve been able to come up with is a food truck. In theory, it’s mobile food service. In practice, it’s either a truck or it’s a kitchen. It can’t be both at the same time effectively.

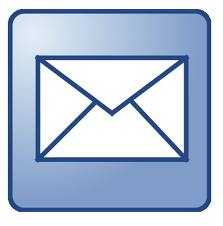





It is great having Joe as part of Beyond Lean. Joe and I spent 4 years working very closely together. It was a great way to learn. We pushed on each other a lot and leaned on each other when necessary. I still reflect on a lot of those learnings today.
ReplyDelete