This year’s Northeast Lean Conference marks a number of milestones in Lean as the conference celebrates its 20th Anniversary. It also marks the 25th Anniversary of Toast Kaizen Video and the 35th Anniversary of the book the Machine the Changed the World. LEAN in conference name is an acronym for Lead Enable and Nurture. The theme this year was about “Leveraging Lean to Thrive in Uncertain Times” which we can all certainly relate to in some way.
“So, You’ve Read 10 Books About Lean and Now You’re
Really Confused? Been There.”
The conference got started with a key note from Brad Cairns,
Lean pioneer and entrepreneur, talked about his life long journey. He started
like many did consuming many books on the subject. He read the Lean Turn Around
by Art Byrne and started down Lean Journey. Learned he couldn’t transform
people so he hired lean consultant named Jim Lewis, Quantum Lean. Read The
Toyota Way and many other books. . Learned from Paul Akers at FastCap, Kaas
Tailor, Michael Althoff at YelloTools, and other great practitioners. He
created Kaizenify.app to bring shopfloor tools to you. He pays it forward through
sharing lesson podcasts, youtube,
etc.
He shared 4 lessons not learned in books that you should
take note of:
1) Preparation – You need to know where are you going and
where you are starting from. You need to know when you’ve made improvements.
The P&L is a poor measuring tool because it last month, last quarter, last
year. Measure forward looking tools (over the line chart, throughput $/labor
hrs, pieces/day)
2) Internal people – You can’t transform donkeys into racehorses.
3) You - Good speech from Jocko
Willink. You can improve from suffering.
4) External People – If you make the change everything will
change. Are your advisors helping you? Lean is for 2% of the world. Go Hard of
Go Home. You pick your hard. Are the people you spend the most time with boat
ankers or propellers? Sometimes you need a kick in the butt or shove in the
right direction.
How Do You Create A Lean Culture? Art Knows
Art Byrne, Wiremold CEO, (where I worked) shares how to Create
a Lean Culture from his newest book “Lean Turnaround Answer Book”. Most significant
steps are below:
1. If given the option no one will choose to do Lean.
Communicate about the change to Lean (what, why, when, how) and what’s in it
for them. Let them know they will not lose their jobs due to improvement. Everything
must change. You can’t have a lean culture without a Lean enterprise involving
every part of the business. Sales & Marketing – level load orders,
Accounting/Finance – standard cost accounting incentives all things we try to
get rid of in lean, IT/Human Resources – hire for lean. Lean is not a cost
reduction program.
2. Lean can not be managed; it must be led. The leader must
be an expert. You can not delegate a Lean conversion. The leader must be hands
on in the Gemba. Leaders should do 12 1-week Kaizens per year to learn about Lean.
2. Requires a new mindset focused on your processes not
results. A company is nothing but these 3 things: A group of people, a bunch of
processes, delivering value to a set of customers.
Set Operational Excellence Goals – What are we Trying to Do
Here?
Wiremold examples:
100% On Time Customer Service
50% reduction in Defects (every
year)
20% productivity gain (every year)
20X inventory Turns
5S and visual Control Everywhere
3. Change Structure – Most companies are organized
functionally. Align your structure with value streams and move the equipment.
4. Kaizen, Kaizen, Kaizen
Create Kaizen Promotion Office. Kaizen includes everyone. Culture
changes through kaizen.
5. State your Core Values: People, Customers, Kaizen
Live by the lean fundamentals
Work to takt time
One piece flow
Standard work
Pull system
Learn by doing = culture change
5. State the Behavior you expect
Respect
others
Tell the
truth
Be fair
Try new ideas
Ask why
Keep your promises
Do your share
6. Eliminate the Bad Actors
7. Share the Wealth
Profit
sharing
401k
match
Suggestion
program
8. Run the company on Operational Excellence Goals. Most run
on make the month. It takes 2 weeks to close the books then you look back at
things you can’t do anything about. Look forward not backwards.
Deploy the Op Ex Goals to the team leaders, review progress
weekly, ask what kaizen are you planning next week, and look forward not
backward.
“If you don’t try something, no knowledge can visit you.”
The Five Factors of Managing Change
Lara Laskowski and Arturo Sanchez from IDEXX understand that
50-70% of change initiatives result in failure but they people they have something
in common. Their organization has a cure for false starts, limited change, frustration,
and very likely another failure. They created a model for Productive Change
involving Vision, Skills, Incentive, Resources, and Action Plans.
Vision – You need a clearly defined vision, problem
statement with who, what, when, where, and why.
Skills – Need SME of the process, create robust training
plan with standards
Incentive – What motivates people to take action, WIFM
Resources – Data needed, software used, people in process,
and budget
Action Plans – Need robust action plan to implement
improvements with ownership.
When elements of the formula are missing you can end up with confusion, anxiety, limited change, frustration, and false starts.
The Magic of Change Mindset with Magician Zane Black
Brad Morrow, The Wizard of Lean, had a wonderfully engaging
presentation to view ourselves as powerful change agents, embrace risks, and
adopt a new view on failure.
There’re three mindsets:
Empowered Mind: Sense of empowerment means you need
to take risk. You miss 100% of the shots you don’t take.
Risk-Taking Mind: The only way to expand your comfort
zone is through discomfort. Embrace fear.
Fear acronym = False, Evidence, Appearing, Real
Failure Embracing Mind: Why do we fall? So, we can
learn to pick ourselves up.
Fail acronym = First Attempt in Learning
Failure is not your last chapter.
If I am Empowered “What Will You Do Next?”
Wiring the Winning Organization
The final keynote of the day was from Steve Spear who has written
Creating High Velocity Organizations and Wiring the Winning Organization. 25
years ago, he wrote “Decoding the DNA the Toyota Production System” which noted
Toyota had created a community of scientists within their organization.
If everything’s the same (resources between car companies)
but the outcomes the only thing different then it’s the management system. They
create conditions to solve really hard problems. As leaders we are responsible
for people solving problems. Shape the problem-solving space to move from
danger zone to winning zone.
There are 3 ways:
1) Slowification – Make problem solving easier to do.
2) Simplification – Make problems easier to solve.
3) Amplification – Make problems more obvious that need
solving
How do we create processes and procedures that allow for
problem solving. 5S, 1 piece flow, Jidoka, and Andon are examples of tools that
move problems from the danger zone to the winning zone.
I’ll share some additional highlights from my 2nd
day at the conference in my next post.
The 21st Annual Northeast Lean Conference will be October 27 & 28, 2025 at the Double Tree Hotel & Conference Center in Manchester, NH.
The 2025 Northeast Lean Conference

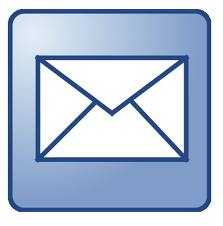




