The end of
the year is traditionally a time to look back and reflect. One way to reflect
is to evaluate popular blog posts. I have been taking time to reflect on the
year that was and as part of that reflection I have flipped back through the 150
blog posts I have written so far this year and compiled a list of my Top 10.
Effective
communication is everyone's job. It builds trust, teamwork, and high-performing
organizations. If culture drives an organization, effective communication is
the fuel.
You should
build your Lean culture on the following essential elements: make the customer
everyone’s business, standardize work for managers, have daily accountability
and require discipline.
As a team
leader, one of your primary roles is developing the resources, specifically,
the human resources of your department, business unit, or team. The tasks of a
team leader are classically defined as those of planning, organizing, staffing,
motivating, achieving, and evaluating results.
Students
participating in an education program at IDEXX Laboratories made a video to
illustrate the 7 wastes.
The effects
of micromanagement can be disastrous for a company’s culture. In the best
situations, micromanagement is an impediment to progress and in extreme cases
it can cause the organization to stagnate.
Kaizen is a
philosophy of continuous improvement in which every aspect of the business can
and must be improved. It is a process that engages the “human element,” while
eliminating all forms of non-value added activity and waste.
The SIPOC is
a key tool to help the team understand and communicate the current state and
the bounds of a given process as well as who might be critical to engage as the
project develops.
In the
office environment, the 8 classic waste types of the Lean methodology manifest
in different ways than we see on the factory floor.
Just because
you are busy does NOT mean you are productive. In this post you’ll learn 6
differences between busy people and productive people.
Daily tiered
meetings (a series of four brief meetings to review what happened yesterday and
assign actions for improvement) are an integral element of daily management
system.
What were
some of your favorite Lean posts from 2017? Any recommendations for next year?

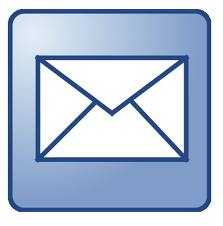




