Who are you and what do you do?
My name is Art Byrne and I am an operating Partner with J W Childs Assoc. a Boston based private equity firm. Prior to that I was the CEO of The Wiremold Company and before that I was a Group Executive for the Danaher Corporation.
How and when did you learn Lean?
I started lean in January of 1982 during my first general managers job at The General Electric Company.
How and why did you start blogging or writing about Lean?
I recently had my book, The Lean Turnaround, published by McGrraw-Hill.
What does Lean mean to you?
To me lean is the greatest strategic weapon any company can use to improve it’s results.
What is the biggest myth or misconception of Lean?
The biggest myth about Lean is that it is just “some manufacturing thing”.
What is your current Lean passion, project, or initiative?
My current lean project is promoting my book.

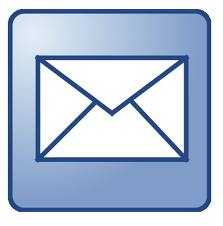




