Click this link for A Lean Journey's Facebook Page Notes Feed.
Here is the next addition of tips from the Facebook page:
Lean
Tip #991 - Get On Board With Change
A
manager must be supportive of a change before he or she can successfully lead
direct reports through the change process. This means that managers and
supervisors have sufficient awareness and desire around the change itself
before they begin engaging their direct reports. To achieve this, the change
management plan must have specific elements aimed at building support with
managers and supervisors.
Lean
Tip #992 – Build Competency for Change
“Leading
change” is a personal competency that managers and supervisors can build. And,
the competency is not necessarily natural. It takes a particular set of skills
to lead a group of employees through a change process. Many times, there are
great managers who struggle in times of change. Appreciating “leading change”
as a unique personal competency and working to build that competency in
managers and supervisors is a critical step, and one that is often overlooked.
Lean
Tip #993 – Provide the Tools Necessary For Change
Managers
and supervisors not only need competencies in leading change, they need tools
to help them help their people in times of change. Many times, the tools needed
to manage change are different than the normal tools managers are familiar with
using. One of the most important tools you can provide to managers and
supervisors is a model for understanding the human reaction to change.
Lean
Tip #994 – Provide Support for Change
Managers
and supervisors will need support when taking on the role of "leader of
change". Some of the tasks and responsibilities that come with being a
good coach of employees through change are difficult. In many instances, this
is a completely new undertaking for a manager or supervisor. You need to
provide outlets and opportunities for support when managers are leading change.
One
area of support necessary will be helping them implement the processes and
tools you have provided for leading change. Opportunities to try out new
approaches for identifying resistance in a safe setting can go a long way in
helping managers and supervisors to be successful.
Lean
Tip #995 - Foster Creative Learning Processes.
Often,
employees want to make suggestions about the way things are done but don't have
a way to voice their ideas. Develop a method that makes it easier for staffers
to share their creative ideas or suggestions with top management.
Lean
Tip #996 - Challenge Employees with Unfamiliar Jobs
Stretch
assignments are growth-oriented exercises with some inherent risk. They’re
designed to push participants past their skill level. Even failure offers
valuable lessons that can add new skills, improve confidence and solidify
employee commitment. You want to give participants first-hand experience in many
different roles throughout your company. They’ll gain exposure to different
divisions and gain new expertise.
Lean
Tip #997 – Practice and Expect Open and Honest Communication
As
a leader, you set the example for how your entire team communicates. Communicate
openly, honestly, clearly, and with the commitment to address the greater good
of your business and those on your team will communicate the same way.
Lean
Tip #998 – Promote Teamwork for Problem Solving
A
quarterback needs his receivers. A pitcher needs his fielders. Even a golfer
needs her caddy. Studies have shown that groups of people working together
produce significantly greater results than people working independently. As a
leader, you need to not just build a great team, but also get your team
actively into the game. Share your vision. Involve others in solving problems.
And delegate responsibilities that allow everyone to contribute to the success
of the organization.
Lean
Tip #999 – Influential Leaders Empower Employees
As
a leader you need to inspire your employees to do more. To improve their
behavior, develop their skills and talents, work better and harder and achieve
great results. Successful leaders understand the importance of influential
leadership and how it impacts employee engagement.
Lean
Tip #1000 – Teach Your Staff To See Problems As Exciting Opportunities For
Improvement
Every
organization has problems. The key is to notice the problems, without dwelling
on the negative. When someone spots a problem, bring your team together to
brainstorm solutions. Point out how you can make changes to make your business
stronger and more successful. And most importantly, don't shoot the messenger.
Recognize and show appreciation for people who bring problems to your
attention.
1000 Tips shared over 5 years, a milestone worth noting. Due to it's popularity I think we shall continue.
Lean
Tip #1001 – Adopt An Open Communication Style
Collaboration
tools compel organizations to become less hierarchical in how they distribute
information. This open communication style allows employees more insight into
what is going on and helps them feel they are part of the business. Those that
don't adapt to this new way of communicating, which tends to facilitate more
transparency and quicker decisions, will be left behind.
Lean
Tip #1002 – Prepare to Adapt to Changes in Communication For Successful
Collaboration
Companies
expend lots of effort vetting collaboration tools and yet too often end up
disappointed in their performance. Technology can be a great tool for
facilitating collaboration, but company culture and management initiative are
still the engine that drives it, especially at the beginning. Many changes are
necessary in workflow and communication style that are frequently not
comfortable for employees to accept. Priming the company to adapt to these
changes is a key factor in facilitating a successful collaboration initiative.
Lean
Tip #1003 - Simplicity is Key for Productive Collaboration.
The
collaboration method must make our jobs more efficient, not create more cycles
of work. A discussion board can often help get the dialogue moving among a
large team, but in some instances it is necessary to pull the discussion away
to a smaller group for a final result.
Lean
Tip #1004 - Craft Simple, Outcome-Oriented Goals
The
more complicated a goal is, the more room for interpretation and extrapolation.
Go the extra mile to make your goals simple and concrete. Outcome-oriented
goals focus on results rather than just products and can provide greater
clarity and focus.
Lean
Tip #1005 - Discuss How the Team’s Goals Tie into the Organization’s.
By
linking a team’s or project’s goals to larger company goals you can find
inspiration and a higher sense of purpose. Everyone on the team will feel they
are playing a meaningful role.

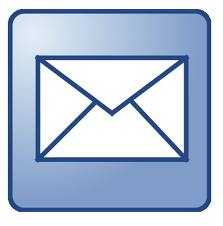




