Observed on the first Monday in September, Labor Day pays tribute to the contributions and achievements of American workers. It was created by the labor movement in the late 19th century and became a federal holiday in 1894. Labor Day also symbolizes the end of summer for many Americans, and is celebrated with parties, parades and athletic events.
Here are 11 interesting facts that you might not know about regarding Labor Day:
- The first celebrated US Labor Day was on Tuesday, September 5, 1882 in New York City, planned by the Central Labor Union.
- 10,000 workers marched from City Hall all the way to 42nd Street and then met with their families in Wendel’s Elm Park for a picnic, concert, and speeches.
- Canada is said to have originated the idea of hosting a day honoring the labor movement. In 1872, they held a “Nine-Hour Movement” to show support for striking workers.
- There is disagreement about who actually proposed Labor Day as a holiday. Some say it was Peter J. McGuire, who was the cofounder of the American Federation of Labor. Others believe that it was Matthew Maguire, a machinist.
- Oregon was the first state to celebrate Labor Day as a legal holiday in 1887.
- The decision to make Labor Day the first Monday of September was approved on June 28, 1894.
- Labor Day started as a part of the labor union movement, to recognize the contributions of men and women in the US workforce, but modernly is seen as a chance to celebrate the last weekend of summer.
- Americans worked 12-hour days seven days a week during the 19th century!
- The Adamson Act was passed on September 3, 1916 to establish an eight-hour work day.
- Historians say the expression “no white after Labor Day” comes from when the upper class would return from their summer vacations and stow away their lightweight, white summer clothes as they returned back to school and work.
- There is still a Labor Day parade in New York City, which takes place throughout the 20 blocks north of the 1882 labor march.
So there you have it. Perhaps a few things you already knew about Labor Day, but hopefully a few that you didn’t.
We celebrate Labor Day because we are all in this world of work together. Let’s enjoy the fruits of our labor and the solidarity of workers, the work we do, and the nation and economy we and our parents and their parents have built. Happy Labor Day!

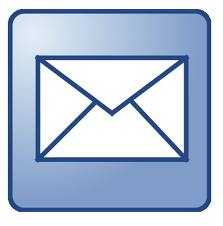




