The successful
implementation of a Lean culture is dependent on management's willingness to
fully involve and engage their workers in the process. So if Lean is about
people the question is what type of people do we want leading the charge. Let’s
look at two types: Firemen and Farmers.
The fireman
works hard in short bursts. As problems fester they turn into a crisis and
flare up. Firemen are need to swoop in a put out the flames. They never know
what they are going to expect until they get to the fire. Firemen focus on
quick actions. Firefighting derives from what seems like a reasonable set of
rules--investigate all problems, for example, or assign the most difficult
problems to your best troubleshooter. But firefighting consumes an
organization's resources and damages productivity.
Firefighting is
popular because it is exciting. Most of us deplore the firefighting style, yet
many managers and organizations perpetuate it by rewarding firefighters for the
miraculous things they do. If the fix works out, the fire fighter is a hero. If
it doesn’t, the fire fighter can’t be blamed, because the situation was
virtually hopeless to begin with. Notice that it is to the fire fighter’s
advantage to actually let the problem become worse, because then there will be
less blame if they fail or more praise if they succeed.
The farmer on
the other hand works constantly from sun up to sun down. Farmers in general take a more steady
approach. The work is predictable and tied to a bigger plan. Farmers take the
long view, and will work for long time to see it through to completion.
Farmers are
shepherds and develop long term relationships. Farmers are patient with others.
The patience that it takes to watch a plant grow for five months is easily
translated into patience with a coworker who wants to explain a problem or
situation.
Farmers are
cautious. Farming doesn’t often demand that a person face short-term danger.
Farmers learn, instead, to face the more long-term dangers. They’re often
better planners than they are fighters.
Implementing
Lean Thinking is a cultural change that requires leadership…because in the end
it’s all about people. What type of person do you want leading your change?
Fireman or Farmer?

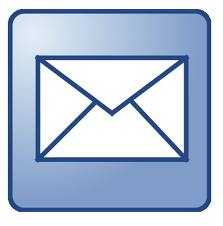




