In order to fully understand Lean and establish the success that can come from truly applying the right thinking it is importance to know how it contrasts with L.A.M.E. The following 10 items are signs of a L.A.M.E. company not a Lean company.
1. Slashing the workforce.
When organizations use lean methods to drive layoffs, this would be an example of L.A.M.E., not Lean. Slash-and-burn approaches send shock waves that affect the remaining workforce. Lean is based on dual ideal of continuous improvement and respect for people. Downsizing is penny-wise and pound-foolish not respectful.
2. Lean is to blame for poor performance.
Low inventories are commonly linked to Lean because many organizations are able to reduce inventory levels due to practicing Lean Thinking. But "true" Lean Thinkers understand lower inventories are a resultant of a process improvement not a solution to a problem.
3. Customers complain often.
Customer responses to your company reflect their treatment by employees, particularly your front-line staff. A lot of complaints means that the customer focused culture you’ve tried to create has either not reached everyone or seems so contrived that customers are dissatisfied rather than delighted.
4. Talented people giving average performance.
Talented people want to deliver great results, not only for your business but also for them. If your star employees are delivering average sales, productivity and profitability, they are not getting what they need from you. Invest in your employees by cultivating continuous learning and improvement.
5. Issues are repeated.
If you hear about the same problems over and over, it's likely that there is little or no effective action being taken to deal with them. This is an indication that there lacks a PDCA approach to problem solving and continuous improvement is probably more like firefighting.
6. Feeling overwhelmed.
No matter how hard you work or how fast you work, you never even come close to getting everything done. It just seems like you've always got too much work and too little time. So you're forced to make one of two unhealthy choices: to either let some work go or let some work get done more poorly than you would like. This is a lack of respect for people.
7. Lack of appreciation.
And this, of course, is one of the worst possible ways to manage or motivate a workforce. Employees at all levels need to know that other people have noticed their good work and have commented on it. Without verbalized appreciation, feelings of "what's the point" and "why bother" start to take over.
8. Disengaged workforce.
Your disengagement can be caused by several things. Your organization may have gone through a huge amount of change but didn't give you any training to cope with the change. So you feel less confident of your abilities. Or the disengagement may have come about because your organization never bothered to learn your strengths or tap into your strengths. Allow employees the opportunity to participate in the business.
9. Hoarding information.
Some people withhold information from others because they know that knowledge is power. And they only share their information when it suits their purposes. In fact, many employees believe their managers know a lot more about the business than they're telling. Remember knowledge is the primary lever that can affect the rate of change in any organization.
10. Unsustainable Results
If a company is focusing on implementing a checklist of tools and processes then they do not understand Lean is about the thinking. These companies are trying to copy and paste solutions that will not fit their needs. I would have to say they are practicing L.A.M.E. if results are not sustaining. A Lean company values standardized work and when implemented the results have a much higher chance of being sustained.
Sometimes it can be hard to tell if a company is Lean or L.A.M.E. For many of us these signs are clear from experience. What other L.A.M.E examples have you seen others claim as Lean?

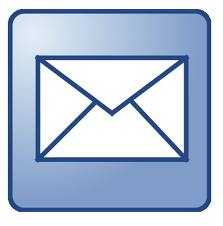





Tim - great list. These are all warning signs for organizations that think they are lean. Someone said that Lean without respect for people is just mean. Your list makes me think of companies who are trying to get lean and efficient without respect for people...companies with these issues are in peril.
ReplyDelete