Click this link for A Lean Journey's Facebook Page Notes Feed.
Here is the next addition of tips from the Facebook page:
Lean Tip #601 - Create a Model Line.
Develop a showplace within your shop where everyone can see how it should be done. Start small, but don't pick a project that has no challenges. Develop key measurements before and after the production line so that people can watch the progress of your get-lean initiative. Finally, create a future-state map that acts as your ideal value stream.
Develop a showplace within your shop where everyone can see how it should be done. Start small, but don't pick a project that has no challenges. Develop key measurements before and after the production line so that people can watch the progress of your get-lean initiative. Finally, create a future-state map that acts as your ideal value stream.
Lean Tip #602 - Learning takes place through the application of lean principles.
Learn as much as possible about a concept, then begin to apply it. A good example is 5S. When 5S is implemented correctly, it not only provides order and improved housekeeping, it also enhances equipment and improves efficiency.
Lean Tip #603 - Visit other successful lean implementations.
It is easy to find companies that will allow you to see their lean implementation. The difficult part is finding a successful implementation. A good way to do this is find a company hiring lean manufacturing professionals. If the implementation wasn't successful, they wouldn't be hiring more professionals.
Lean Tip #604 - Encourage creativity by thinking differently and rewarding good ideas.
If you want to hear the best ideas about your business, give an incentive to get them heard. Make sure you reward creativity and thinking differently, not just whether an idea will work or not. What you want is the culture that allows ideas and challenge – in that culture not every idea will be successful, but at least they are being raised.
Lean Tip #605 - Get out there, go to the gemba.
I say this to executives and to on-the-floor people alike. They must start their Lean journey with a trip to see what Toyota calls the three reals - the real place, the real data and the real problem. They must go and see for themselves, not just take the advice of a Lean committee!
I say this to executives and to on-the-floor people alike. They must start their Lean journey with a trip to see what Toyota calls the three reals - the real place, the real data and the real problem. They must go and see for themselves, not just take the advice of a Lean committee!
Lean Tip #606 - Think about how to do it, not why it can't be done.
I often hear, "We tried that before and it didn't work." They may have had a good idea, but the chances are that they didn't include the accountability portion. Without accountability, you will not have sustainability. Make someone accountable and avoid the "flavor of the month."
I often hear, "We tried that before and it didn't work." They may have had a good idea, but the chances are that they didn't include the accountability portion. Without accountability, you will not have sustainability. Make someone accountable and avoid the "flavor of the month."
Lean Tip #607 - Do not seek perfection. Do it right away.
Taiichi Ohno used to regularly nag at people not to let a quality problem "escape" to the next customer. You've got to stop what you're doing, put a countermeasure on it and do it right away.
Taiichi Ohno used to regularly nag at people not to let a quality problem "escape" to the next customer. You've got to stop what you're doing, put a countermeasure on it and do it right away.
Lean Tip #608 – We don't have bad people, just bad processes.
For the most part, this is true. By concentrating on the process and building continuous improvement there, you will have the culture change that you're looking for.
For the most part, this is true. By concentrating on the process and building continuous improvement there, you will have the culture change that you're looking for.
Lean Tip #609 - Question everything.
Ask "why" five times. A brilliantly simple root cause problem-solving tool, asking why five times becomes easier the more you do it. Adopting this as a default way of looking at things will aid, not only your problem solving, but other areas, too.
Ask "why" five times. A brilliantly simple root cause problem-solving tool, asking why five times becomes easier the more you do it. Adopting this as a default way of looking at things will aid, not only your problem solving, but other areas, too.
Lean Tip #610 - Get support from the senior management.
Lean's successes are 20 percent due to the tools. About 80 percent comes from culture change, which is driven by support from senior management. Without this, Lean will be just another fad. Take no action and nothing will happen. If you do nothing, nothing changes. Be aware of items that stall your action. It's better to have a 50-percent reduction in waste right away than it is to take no action and hope for a 100-percent reduction in waste sometime in the future.
Lean's successes are 20 percent due to the tools. About 80 percent comes from culture change, which is driven by support from senior management. Without this, Lean will be just another fad. Take no action and nothing will happen. If you do nothing, nothing changes. Be aware of items that stall your action. It's better to have a 50-percent reduction in waste right away than it is to take no action and hope for a 100-percent reduction in waste sometime in the future.
Lean Tip #611 - Kaizen requires a bias for action.
Get your teams out of the conference room and into the gemba. From there, mandate a fast turnaround time, have them quickly do a value stream map and root cause analysis for their actionable items, and post their successes right away.
Get your teams out of the conference room and into the gemba. From there, mandate a fast turnaround time, have them quickly do a value stream map and root cause analysis for their actionable items, and post their successes right away.
Lean Tip #612 - Kaizen starts with taking a look at the actual place of work.
Continuous improvement efforts must start with a trip to the gemba. The gemba might often be the factory floor, but people forget about Lean in the office, where half of the work starts out being late! It's easy to see waste on the floor, but it's harder (at first) to see waste in the office or other value streams. Going to the gemba will make it easier.
Continuous improvement efforts must start with a trip to the gemba. The gemba might often be the factory floor, but people forget about Lean in the office, where half of the work starts out being late! It's easy to see waste on the floor, but it's harder (at first) to see waste in the office or other value streams. Going to the gemba will make it easier.
Lean Tip #613 - Do not spend money for kaizen.
All that proves is that you have a lot of money. It doesn’t matter whether you're in manufacturing or health care, you don't have "extra" money. Toyota says that they use their wits, not their wallets, for continuous improvement.
All that proves is that you have a lot of money. It doesn’t matter whether you're in manufacturing or health care, you don't have "extra" money. Toyota says that they use their wits, not their wallets, for continuous improvement.
Lean Tip #614 – Take no action and nothing will happen.
If you do nothing, nothing changes. Be aware of items that stall your action. It's better to have a 50-percent reduction in waste right away than it is to take no action and hope for a 100-percent reduction in waste sometime in the future.
If you do nothing, nothing changes. Be aware of items that stall your action. It's better to have a 50-percent reduction in waste right away than it is to take no action and hope for a 100-percent reduction in waste sometime in the future.
Lean Tip #615 - Show results, not action items.
It's terribly important that you post real results on your Lean board, not things that you're going to do. You must be able to point out your successes if you're ever going to convince the CAVE people that Lean works. (CAVE = Citizens Against Virtually Everything)
It's terribly important that you post real results on your Lean board, not things that you're going to do. You must be able to point out your successes if you're ever going to convince the CAVE people that Lean works. (CAVE = Citizens Against Virtually Everything)

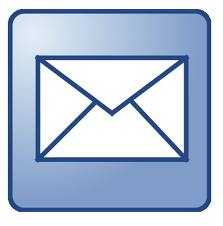





No comments:
Post a Comment