Click this link for A Lean Journey's Facebook Page Notes Feed.
Here is the next addition of tips from the Facebook page:
Lean
Tip #811 - Share Successes Within Your Company
One
of the best parts about creating an environment that fosters collaboration and
experimentation is sharing successes and failures so that everyone can learn
from it. When you do something that you consider a success such as developed a
new app or even a new strategy that was effective, share it. Not only can it
benefit the community at large but it will make your staff feel recognized and
feel that they are contributing to something bigger.
Lean
Tip #812 - Commit to Culture Change and Failing Fast
While
creating a culture of collaboration and innovation within a very traditional
and rigid organizational structure can be challenging it can definitely be
achieved. But, make no mistake it requires a major culture change within the
entire organization that must be led from the top. Senior management must focus
on breaking down the silos in the organization to have more of an open culture
and leadership.
Lean
Tip #813 - Celebrate the Work of Others.
Celebrate
your successes! Find ways to publicize your ongoing collaborative work, giving
credit to those who have taken on new roles. As projects draw to a close, focus
on the ways collaborative work has enhanced the customer and company. Use your
celebrations to recruit new supporters and fortify future collaboration. In
this way, collaboration becomes rooted in the company’s culture.
Lean
Tip #814 - Keep Your Organizational Hierarchy as Flat as Possible to Foster
Collaboration.
The
more layers and levels of management, team leaders division heads, etc., that
you have in your company, the more challenging it becomes for information to
travel throughout the organization, and the more people are likely to become
territorial. BY keeping the layers of information to minimal we can empower
people to provide solutions and to be directly attached to all of our company
goals.
Lean
Tip #815 - Push Decision Making Down
Try
to push decision making down to the lowest level of your organization. If you
allow the people in your company who are directly connected to the problems that
emerge, to be able to make decisions to fix those problems, you typically will
get the best solutions. More succinctly put, the people who encounter the
problems all of the time, usually know the best ways to fix the problems. We
know that if you do not empower those who encounter the problems to be able to
make decisions in how we fix them, then ultimately everyone just develops
"work arounds" and the problem gets greatly delayed in being
resolved.
Lean
Tip #816 - Establish the Core Values that Comprise the Continuous Improvement Culture.
Establish
the core values that comprise the continuous improvement culture such as a
focus on supporting the customer, teamwork throughout the extended enterprise,
receptivity to evolving continuous improvement concepts and tools. These core
values will create a sense of belonging and a common vision for all involved.
Lean
Tip #817 – Regular Communication Fosters Collaboration
Ensure
regular communications to foster collaborative interactions among leaders,
stakeholders, and practitioners at all levels.
Where needed, schedule face to face meetings and where not needed, use
the communication and collaboration tools and capabilities of the enterprise to
keep all members updated and involved.
Lean
Tip #818 - Use a Consistent Approach for Projects
A
consistent and structured approach for project identification and execution
will provide the organization with the ability to identify, select, and manage
continuous improvement projects. It should also provide post-closing process
steps to continually refine the improvement project methodology and to act upon
the lessons learn from the project effort.
Lean
Tip #819 - Facilitate Process-Centric Thinking
Process-centric
thinking does not have to be overly complex. Sometimes, all it takes is a
thoughtful examination to uncover significant areas for improvement. Rather
than tolerating mistakes and repeat errors, facilitate process-centric thinking
to continually improve, correct, and overcome execution difficulties.
Lean
Tip #820 - Turn Employees into Problem Solvers and Improvement Specialists
The
most important aspect of lean is to involve employees in developing lean
processes. Many times companies create a culture in which the employees don't
make the decisions, management does. Then when problems occur, employees are
unable to diagnose or solve problems without involving a supervisor. lean
reverses that by revolving around employees and looking to them as the
improvement specialists.
Lean
Tip #821 - Measure, Audit, Review and Continue to Improve Processes
A
common saying with our lean program is, “If you can't measure, you can't
improve.” Without a baseline, you will not be able to show improvements, so you
must measure virtually every process.
Use
audits to not only sustain the improvements from Kaizen, but also expose new
problems and resolve them with your employees' involvement and input.
Create
a culture that continually looks to improve processes — even ones that aren't
broken. Through lean you will learn to look at things differently and develop
an eye for improvement. The key is to get as many “eyes for improvement” as
possible.
Lean
Tip #822 - Teach Others What You Learn.
One
of the best ways to deepen and solidify your new knowledge is to teach it to
others. Give a presentation, run a seminar, teach a class, or volunteer to run
a small internal workshop to teach others in your organization what you are
learning. Real learning occurs when you share it.
Lean
Tip #823 - Focus on the Big Picture
Explain
the long-range plans of the company and reinforce them regularly. People often
become so focused on today's problems and routine duties that they lose sight
of the big picture. When some members of the team concentrate on putting out
fires, others can dedicate more time to reviewing processes to eliminate future
problems.
Lean
Tip #824 - Create a "We" Culture
Team
building starts at the top. If senior executives encourage an environment where
the organization uses less "I" and more "we" in how they
communicate, everyone will feel supported, included and important to the
organization. This eliminates an employee's fear of standing alone and shows
that the entire organization is thinking about the company.
Lean
Tip #825 - Recognize Success, Regardless of Its Origin
The
worst organizations are those that think good ideas or successful programs only
come from senior-level individuals. Conversely, good organizations encourage
creative thinking from all levels and give credit when a creative idea or
solution comes from junior or mid-level employees. This is one of the most
crucial components of developing a teamwork-based culture.

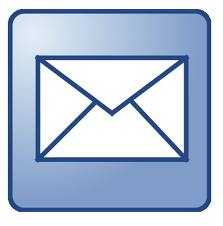





No comments:
Post a Comment