In manufacturing, changeover is the process of converting a line or machine from running one product to another. Changeover times can last from a few minutes to as much as several weeks in the case of automobile manufacturers retooling for new models.
Reducing
changeover time is like adding capacity, increasing profitability and can help
most manufacturers gain a competitive edge. Image a pit crew changing the tires
on a race car. Team members pride themselves on reducing changeover by even
tenths of a second because it means that their driver is on the road faster and
in a better position to win. The same philosophy applies to manufacturing – the
quicker you are producing the next scheduled product, the more competitive you
are.
The
purpose for reducing changeover time is not for increasing production capacity,
but to allow for more frequent changeovers in order to increase production
flexibility. By reducing changeover
times, your company will be able to run smaller batch sizes. If being able to
offer a mix of products and services is important, then quick changeover will
reduce the number of operations you need to run every day, week, or month.
The
benefits of quick changeover include:
- Reduce defect rates - Quick Changeover reduces adjustments as part of setup and promotes quality on the first piece.
- Reduce inventory costs - Elimination of, or reduction in numbers of batches, and their sizes, allows for recovery of operating cash and manufacturing space.
- Increase production flexibility - Increase output and improve timeliness of response to customer orders.
- Improve on-time delivery - Quick Changeover supports the ability to meet customer demands.
The
keys to quick changeover are found in changing your thinking about changeover
as in the following:
- Rethink the idea that machines can be idle, but workers cannot be idle.
- The ideal setup change is no setup at all or within seconds.
- Ensure that all tools are always ready and in perfect condition.
- Blow a whistle and have a team of workers respond to each changeover.
- Establish goals to reduce changeover times, record all changeover times and display them near the machine.
- Distinguish between internal and external setup activities and try to convert internal to external setup.
To
start identify and separate the changeover process into key operations –
External Setup involves operations that can be done while the machine is
running and before the changeover process begins, Internal Setup are those that
must take place when the equipment is stopped.
Aside from that, there may also be non-essential operations. Use the
following steps to attack the quick changeover:
Eliminate
non-essential operations – Adjust only one side of guard rails instead of both,
replace only necessary parts and make all others as universal as possible.
Perform
External Set-up – Gather parts and tools, pre-heat dies, have the correct new
product material at the line… there's nothing worse than completing a
changeover only to find that a key product component is missing.
Simplify
Internal Set-up – Use pins, cams, and jigs to reduce adjustments, replace nuts
and bolts with hand knobs, levers and toggle clamps… remember that no matter how
long the screw or bolt only the last turn tightens it.
Measure,
measure, measure – The only way to know if changeover time and startup waste is
reduced is to measure it!

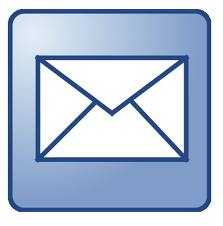





The same philosophy applies to manufacturing – the quicker you are producing the next scheduled product, the more competitive you are.
ReplyDelete