Click this link for A Lean Journey's Facebook Page Notes Feed.
Here is the next addition of tips from the Facebook page:
Lean
Tip #826 - Connect Business Objectives And Individual Metrics
Performance
metrics should have one goal – to help an organization contribute to overall
company success. But too often at the working level, metrics are random and
disconnected from strategic imperatives.
Lean
Tip #827 - Implement Discipline And A Meaningful Quality Program
Develop
a quality program that promotes organizational and individual accountability to
drive improvements. Reliable metrics will take out the guesswork and allow for
management based on facts – not assumptions. Use the program to establish
reward systems and corrective actions to proactively address issues, fine tune
training and ensure that the customer remains number one.
Lean
Tip #828 – Make Metrics More Actionable
Metrics
at the lowest layer of an initiative or organization have the highest
actionability. A focus on the most actionable metrics is essential for ‘moving
the needle’ of big-picture metrics.
Lean
Tip #829 – Too Many Metrics Leads To Too Little Action
It
may seem a little obvious, but a large number of companies go to the trouble of
designing metrics and buying expensive tools, and then do not actually do very
much with the results. Usually it is because too many metrics have been set. So
keep it manageable – it is better to have five meaningful metrics that the
organization will use than 50 that it won’t.
Lean
Tip #830 - Do Not Forget The “Continual” Part Of Improvement
When
implementing metrics, don’t forget that the organization will need to revise
its metrics from time to time. The process is needed because businesses evolve
and changes will surface as time goes by. Make sure the metrics still measure
what they intended to measure. After all, if the metrics are out of date, then
what is the purpose of retaining them?
The
aim of a setting metrics is to improve the business, so set targets that
challenge the company. It will provide more value than focusing on something
that is easily achievable or is already being achieved and remember, what you
can’t measure, you can’t control.
Lean
Tip #831 - Point Employees in the Right Direction.
Help
your employees understand how their roles play into the company’s ability to
succeed. Remind workers that—like members of a football team, for example—each
player must focus on doing their best on the on activities within their reach
that effectively push the ball closer to the end zone. Again, ensure that
workers know where to focus so that they are always contributing effectively on
corporate strategies.
Lean
Tip # 832 - Don’t Forget to Course-Correct.
Everyone
can relate to times when coworkers were heads down on a project that had no
real purpose. But in rough economic times, no organization can afford to
squander resources on busywork. Every effort expended by your workforce should
be purposeful and tied to corporate goals. Prioritize only those activities
that are strategically pertinent, and ensure that non-strategic activities
don’t creep into the picture. If employees do become sidetracked, refer to
cascading goals to pinpoint the problem, and refocus efforts toward tasks that
are higher in priority.
Lean
Tip #833 - Keep Goals on Track.
No
strategy is set in stone, which makes the goal setting process a dynamic endeavor.
Consider yourself a coach on the sidelines, continuously referring to playbooks
and constantly re-evaluating strategies and players or making adjustments at
halftime. Set goals, and execute on them—but be sure to evaluate those goals
year-round, not solely during performance reviews. The more you monitor
individual objectives, the greater the likelihood that they will be on target
and fulfilled.
Lean
Tip #834 - Focus Action-Planning on Daily Activities.
Increasingly
heard at major corporations is the need to "just show them what to
do". Remember that simplicity can quickly alleviate confusion surrounding
what employees are now expected to do. There are powerful best practices
already in place inside the company—sharing them broadly in employees' own
words will go far.
Lean
Tip #835 - Communicate Clearly and Collaborate on Goals and Objectives
In
too many cases, goals and objectives are finalized by executives without
speaking to anyone working in the trenches.
Opening the lines of communication between the c-suite and the ground
floor will help to highlight issues and concerns. It will also give employees a better
understanding of the company’s overall strategy and how they fit in.
Lean
Tip #836 – The First Step To Improvement Is To Recognize The Problem
Continuous
Improvement is the ongoing effort of engaged employees and improvement teams to
improve information, materials, products, services or processes.
The
first step in establishing a continuous improvement mind set is to recognize
the problem. That is, recognize the fact that your organization does not have
or could do quite better exhibiting a continuous improvement mind set.
Lean
Tip #837 – Establish An Enduring Culture
Adaptability
and an action oriented leadership team are inherent components of a continuous
improvement culture. Resistance to change exists in all organizations to a
degree and it must be recognized for what it is, an impediment to improvement.
Lean
Tip #838 – Think Kaizen and Cross the Chasm
Many
people advocate Kaizen oriented thinking and behavior where continual small,
incremental improvements provide tremendous benefits in performance and end
results achieved over time. Others advocate a Crossing the Chasm mind set where
drastic change is introduced completely replacing inefficient execution rather
than slightly improving upon it. In a continuous improvement culture, there is
room for both approaches.
Lean
Tip #839 – Facilitate Process-Centric Thinking
Process-centric
thinking does not have to be overly complex. Sometimes, all it takes is a
thoughtful examination to uncover significant areas for improvement. Rather
than tolerating mistakes and repeat errors, facilitate process-centric thinking
to continually improve, correct, and overcome execution difficulties.
Lean
Tip #840 - Educate The Workplace
Expect
and overcome resistance to change with ongoing training, reinforcement of
expected behaviors, and recognition of those who are learning and doing.

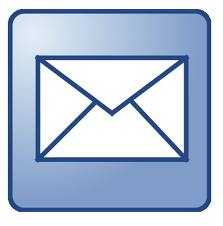





No comments:
Post a Comment