In order to gain a competitive edge, many companies have adopted lean manufacturing (or lean thinking) as a keystone for success in today’s global market. Lean manufacturing has enabled businesses to increase production, reduce costs, improve quality, and increase profits by following key principles:
Identify Value
The first principle of lean manufacturing pertains to
defining value. It is important to understand what value is before anything
else within the process. Value is what the customer is willing to pay for. It
is important to discover the actual needs of the customers. At times, the
consumer may be unable to properly articulate what exactly they want, which is
common in areas of novel products or technology.
Continuous Flow
Efficient product flow requires items to move from
production to shipping without interruption and can be achieved by
strategically organizing the work floor. Every factor, from people and
equipment to materials and shipping, must be taken into account to ensure
products seamlessly move through the production process.
Create Pull
Inventory is one of the biggest wastes within a production
facility. The overall goal of a pull-based system is to limit inventory and
work in process (WIP) items while ensuring that the requisite materials and
information are available for a smooth workflow. A pull-based system allows for
Just-In-Time delivery and manufacturing where products are created at a time
they are needed and in the quantities needed.
Level the Work
One of the foundational lean principles of lean
manufacturing is levelized production. The basis of this principle is that the
workload is the same (or level) every day. Most manufacturing companies are at
the mercy of their customers for orders. Before producing product, they wait to
get orders. This leads to increased delivery lead time which may not satisfy
customer requirements.
Eliminate Waste
Waste in the value stream is any activity, which the
customer is not willing to pay for since it adds no value to the product or
service and often, is consuming resources. The waste can be broken into two
categories: non-value added but necessary and non-value & unnecessary. The
later is pure waste and should be eliminated while the former should be reduced
as much as possible. Waste exists in all parts of the business – front office
to the factory.
Kaizen Mindset
Kaizen, a philosophy of continuous improvement, can help
businesses with this shift by creating a culture where workers seek perfection.
Kaizen focuses on making small, incremental changes and requires every worker,
from the corner office to the production floor, to help improve business
practices. Over time, Kaizen will result in increased efficiency, lower costs,
greater productivity, and better quality products.
Visualize Problems
Visual management aims to make the situation easily
understood merely by looking at it. The goal is to get as much information as
possible with as little observation or time as possible. Visual management is
used to share information, work standards, build on those standards, highlight
problems, stop problems occurring and prevent problems altogether. If visual
management has been done well, everyone in your factory understands and knows
how to fix an issue if something is wrong. Visual management complements well
with the idea of going to the real place.
Stop and Fix
It’s so easy to just ignore problems when they pop up
because they keep you from being productive. Truth be told, it’s easier in the
long run to stop and fix the issue right away because you’ll be doing whatever
is necessary to make sure the problem will NOT re-occur.
Use root cause analysis and the five-whys to figure out why
a problem occurs, figure out what can be done to make sure the problem won’t
come back, and make that fix. The more you attack problems and fix them, the
more the organizational culture will begin to see the simplicity in doing so
and the benefits realized by not having as many breakdowns or repeated repairs.
This will build momentum toward a change in culture of not tolerating problems
and continuous repairs.
Creativity Before Capital
Simply put, this principle demands that we think more about
making our improvements by utilizing what is nearby without spending capital
dollars. Dr. Shigeo Shingo preached to engineers not to become a "Catalog
Engineer". Catalog Engineers spent all of their time looking for solutions
in a catalog and buying a quick fix. He would say to throw out the catalog and
go to gemba. Creativity before capital is the lost principle of lean in
America.
Standardize Work
Standardized work is the name given in lean manufacturing
for documenting the steps of a job task and the sequence in which those should
be performed. You can think of standardized work as defining who does the task,
when they do it, and how they do it.
The documentation of standardized work should be done in a
collaborative process with people who actually do the job task as part of their
job as well as others–including perhaps engineers and supervisors.
Standardizing the work adds discipline to the culture, an
element that is frequently neglected but essential for lean to take root.
Standardized work is also a learning tool that supports audits, promotes
problem solving, and involves team members in developing poka-yokes.
Built in Quality
Another key lean manufacturing principle is Quality Built
In, or Jidoka. The idea behind this principle is that quality is built into the
manufacturing process. Quality is built into the design of the part. Quality is
built into the packaging. Throughout all areas of the product, from design to
shipping, quality is built into the process.
Jidoka builds quality into the process through detection or
prevention. Each lean manufacturing
process will be designed to highlight any abnormality so that the employee can
stop the process. Stopping the process
so that the problem can be fixed is a key part of the Jidoka lean principle.
Develop People
In order to fully realize potential, you’ll have to add
knowledge, skills, and experience. Don’t expect your people to do their best if
you don’t equip them with the training they need to perform. And don’t expect
your potential to spring forth in a final draft; it takes time to hone your
skills and build your confidence. This could come from formal schooling, from
the school of hard knocks, or from both. Either way, your education is the
house your realized potential will live in.
Develop exceptional people and teams who follow your
company's philosophy Empowerment happens when employees use the company tools
to solve problems. Build cross functional teams to improve quality and
productivity. Work hard to reinforce the company culture and assure it is
followed over the course of years.
Respect for People
The most valuable resource to any company are the people who
work for it. Without the people, businesses do not succeed. The respect for
people principle is made up of Respect and Teamwork. This approach allows the company to leverage
and utilize the collective problem solving capability of the employees to drive
improvement. Most people want to perform well in their jobs. The employees want
to earn a decent living and have a sense of worth while working. They want to
feel like they have contributed to the company goals, like their work and
effort has meant something.
Go See For Yourself
Data can tell you a lot of the story, but it can’t tell you
the whole story. Going to see the process or activity yourself lets you gain a
better understanding of what’s truly happening, information that can transcend
the data. Solve problems and improve processes by going to the source and
personally observing and verifying data rather than theorizing on the basis of
what other people or the computer screen tell you.
Seek Perfection
While seeking perfection may seem straightforward, it is
often one of the most difficult principles to successfully apply in the
workplace. Seeking perfection requires companies to continuously improve their
practices and often requires a shift in the workplace culture. All employees
should attempt to strive toward perfection while delivering products based on
the customer needs.
These principles of lean manufacturing can help companies to
operate more efficiently. Implementing lean concepts is beneficial for the
bottom line since greater efficiency leads to better profitability. It also
creates a positive customer experience which improves overall satisfaction and
enhances your brand’s reputation.

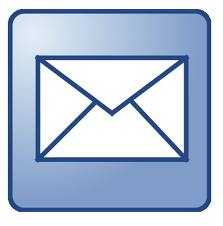





No comments:
Post a Comment