The second annual MFG Day event, is just around the corner. Scheduled for October 4, 2013, the event aims to address common misconceptions about manufacturing through coordinated open houses across the United States. MFG Day is designed to address the skilled labor shortage and connect with future generations while simultaneously improving the public image of manufacturing.
Recent
global surveys reflect the widespread industry challenge. A 2012 McKinsey &
Company report revealed that while most of the young people surveyed (70
percent), admitted that they believe vocational schools are more helpful in
getting a job than an academic track, two-thirds also said that vocational
education is “less valued” in society than other academic paths. And only 30
percent of parents encourage their children to consider manufacturing careers.
MFG
Day is an important part of efforts to support the future of manufacturing here
in the US. As manufacturers today, we know that negative, untrue stereotypes
plague our sector and drive young people away.
We know that we have to overcome the perception that manufacturing jobs
are dirty, dangerous dead ends. We know
that we must spread the word that manufacturing has gone high tech, with
modern, clean facilities, computers, robot, and automation. We know that counteracting outdated, negative
images with current, positive ones is the best way to fight problems like the
skills gap that threaten the American manufacturing sector's recent boom.
And
MFG Day is just the way to do what we know we must. MFG Day gives manufacturers
around the country the opportunity to open their doors to local school kids,
parents, community college students, job
seekers and members of the media so that they can see firsthand the safe,
high-tech and innovative work environments that await the best and brightest
who pursue careers in manufacturing.

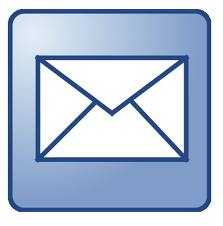




