A key part of
Lean (or continuous improvement) is continuous education – learning new ideas
to challenge your thinking. The Lean community of thinkers is a generous one
that believes in paying it forward. Many share their knowledge and experience
in blogs they write. Reading these Lean blogs can keep Lean principles and
practices at the forefront of your mind as you make decisions in work and in
life.
Here’s a list
of ten Lean blogs you should follow, in no particular order…
1) Bobemiliani.com – by Bob Emiliani
Location: Providence, Rhode Island
About: Bob Emiliani is a professor of
Lean management at Central Connecticut State University. He is an author of 17
books and 47 research papers based on his deep researches in the fields of
leadership and management. Prior to his academic career, Dr. Emiliani has 15
years of industry experience and he is more than passionate about Lean management.
All this knowledge converts into insightful articles presented in his blog. A
gold mine for both, Lean practitioners and Lean enthusiasts.
Frequency: 7 posts / month
2) Curious
Cat Management Improvement Blog –
by John Hunter
Location: Houston, TX
About: In Curious Cat, John Hunter shares
opinions and challenges derived from his professional and personal experience.
John is an author, lean management practitioner, software development
consultant and much more. Here you can find original commentaries related to
different topics such as lean management, management improvement and etc.
Frequency: 3 posts / day
3) Gemba
Academy Blog –
by Jon Miller, Ron Periera, Kevin Meyer, Steve Kane
Location: USA
About: Gemba Academy offers online Lean
Manufacturing, Lean Office, and Six Sigma training to companies around the
world. They teach topics such as 5S, the 7 Wastes, Kanban, Standard Work, Value
Stream Mapping, Quick Changeover, and how to leverage these methods in Kaizen
Events.
Frequency: 2 posts / week
4) JFlinch
Blog – by
Jamie Flinchbaugh
Location: Lehigh Valley, PA
About: Jamie Flinchbaugh is a lean
advisor, speaker, and author. He has advised over 300 companies around the
world in a lean transformation. Previously he co-founded the Lean Learning
Center, and he has helped build nearly 20 other companies as either a
co-founder, board of directors member, advisor, or angel investor.
Frequency: 3 posts / week
5) Lean
Blog – by
Mark Graban
Location: Fort Worth, TX
About: Mark started this blog back in
2005. He is a veteran Lean management practitioner in the manufacturing
industry and later he decided to dedicate his professional life to
incorporating the principles of Lean in the healthcare industry.
Frequency: 1 post / day
6) Lean
Pathways –
by Pascal Dennis and Al Norval
Location: Toronto, CA
About: In this outstanding Lean blog, you
can enjoy insightful articles, find interesting facts and curious points of
view. The author often presents commonly accepted norms and theories related to
Lean but from a different angle. Pascal Dennis is a professional engineer,
advisor and author of several books. He has a solid background with Lean and
has supported lean implementation at leading international companies from
different industries.
Frequency: 1 post / week
7) The
Lean Thinker –
by Mark Rosenthal
Location: Washington
About: Mark is seasoned in lean
manufacturing and has more than 20 years of professional experience. He has
helped various organizations to implement and understand continuous
improvement. Whether you are a beginner or an advanced professional, in this
Lean blog you may find valuable information about broad or more specific
topics.
Frequency: 1 post / week
8) Katie
Anderson Blog –
by Katie Anderson
Location: Massachusetts
About: For over 20 years, Katie has
helped thousands of leaders around the world develop the mindset and
capabilities to create organizational learning cultures that foster innovation,
engagement, and longevity. She’s on a mission to empower leaders at all levels
to lead with intention to achieve higher levels of performance, increase their
personal and professional impact, and create a meaningful legacy.
Frequency: 1 posts / month
9) Old
Lean Dude –
by Bruce Hamilton
Location: Massachusetts
About: Bruce has been around the Lean
scene since 1985, first as a practitioner and later as a consultant. He is
passionate about learning and shares all his thoughts and learned lessons on
his blog. As he says “Everyday there is something new to learn and to share.”
His blog is an ongoing reflection on Lean philosophy and practices with an
emphasis on keeping good jobs close to home.
Frequency: 1 post / week
10) A
Lean Journey –
by Tim McMahon
Location: Massachusetts
About: Tim is a Lean implementation
leader, author, and blogger. Tim has more than 20 years of leadership
experience implementing Lean manufacturing. A proven leader in high tech
manufacturing companies, he is passionate about quality improvement methods by
actively learning, thinking and engaging people.
Frequency: 3 posts / week
Note: I know
this is my own blog, but I am partial to my own labor of love.
Bonus:
The Lean Post – by The Lean Enterprise Institute
(collection of authors)
Location: Worldwide
About: LEI brings together authors from around
the world sharing articles about making the world better through lean thinking
and practice.
Frequency: 3 posts / week
KaiNexus Blog – by The KaiNexus Team (collection of
authors)
Location: Texas
About: This blogs brings shares articles from
KaiNexus consultants who’s mission is to use their technology and experience to
foster and help spread continuous improvement.
Frequency: 3 posts / week
The blog
landscape has changed a lot over the last decade and likely will continue to
evolve. I have chosen to focus on personal blogs here, my preference. Yet,
there are many other helpful Lean blogs that are not on this list. Let me know
the blogs that you enjoy reading.

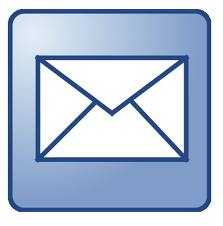




